Workforce Management Software for Food Processing
Simplify your workforce management with automated scheduling that adapts to consumer packaged goods (CPG) production needs in real-time. Ensure compliance, improve efficiency, and boost frontline worker satisfaction with our comprehensive solution.
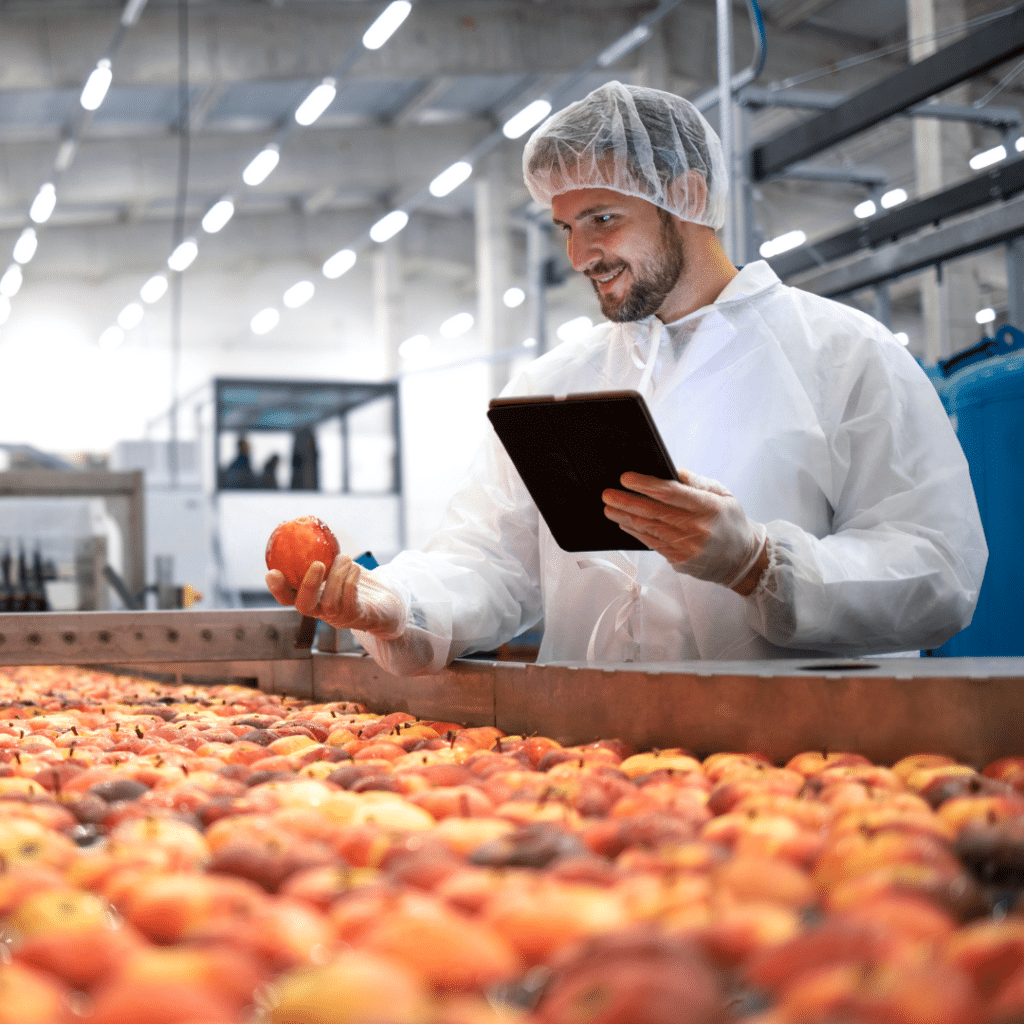
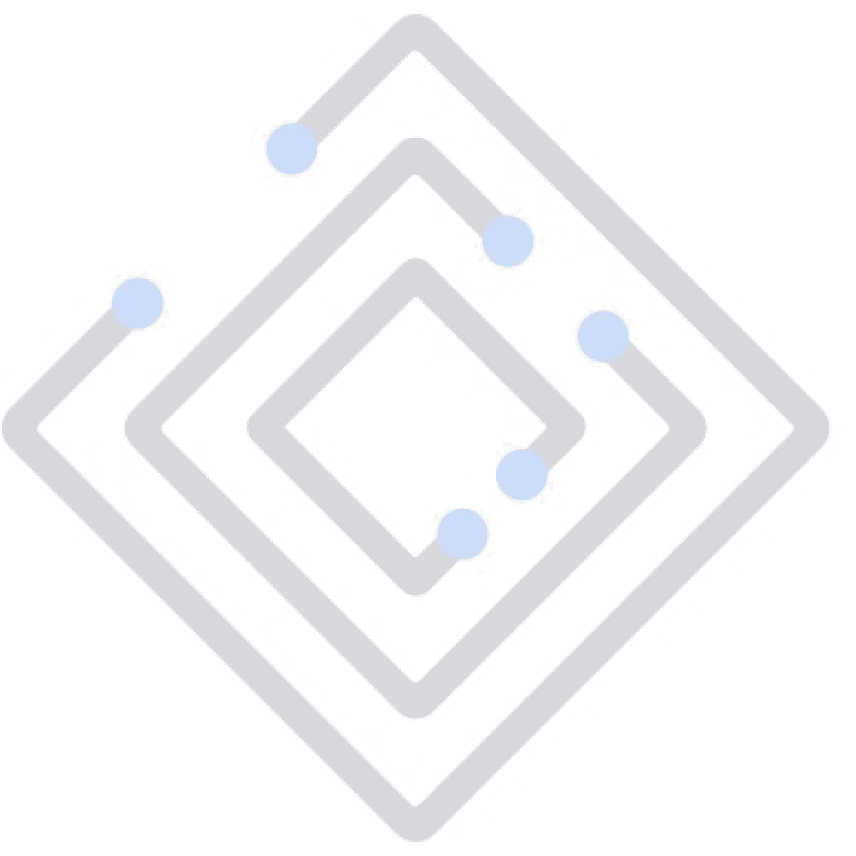
Trusted by the world's most mission-critical enterprises
of manufacturing employees regularly work overtime hours
of overtime in manufacturing is unbudgeted
of the scheduling process can be automated, resulting in the elimination of data entry errors
Automatically Generate a Schedule that Accounts for it All
Indeavor provides a streamlined scheduling solution, optimizing workforce allocation to meet production demands.
- Optimize production around seasonality and availability of ingredients
- Significantly reduce the time spent building employee schedules
- Adjust for seasonal changes in demand for finished products
- Avoid both under- and over allocation of labor
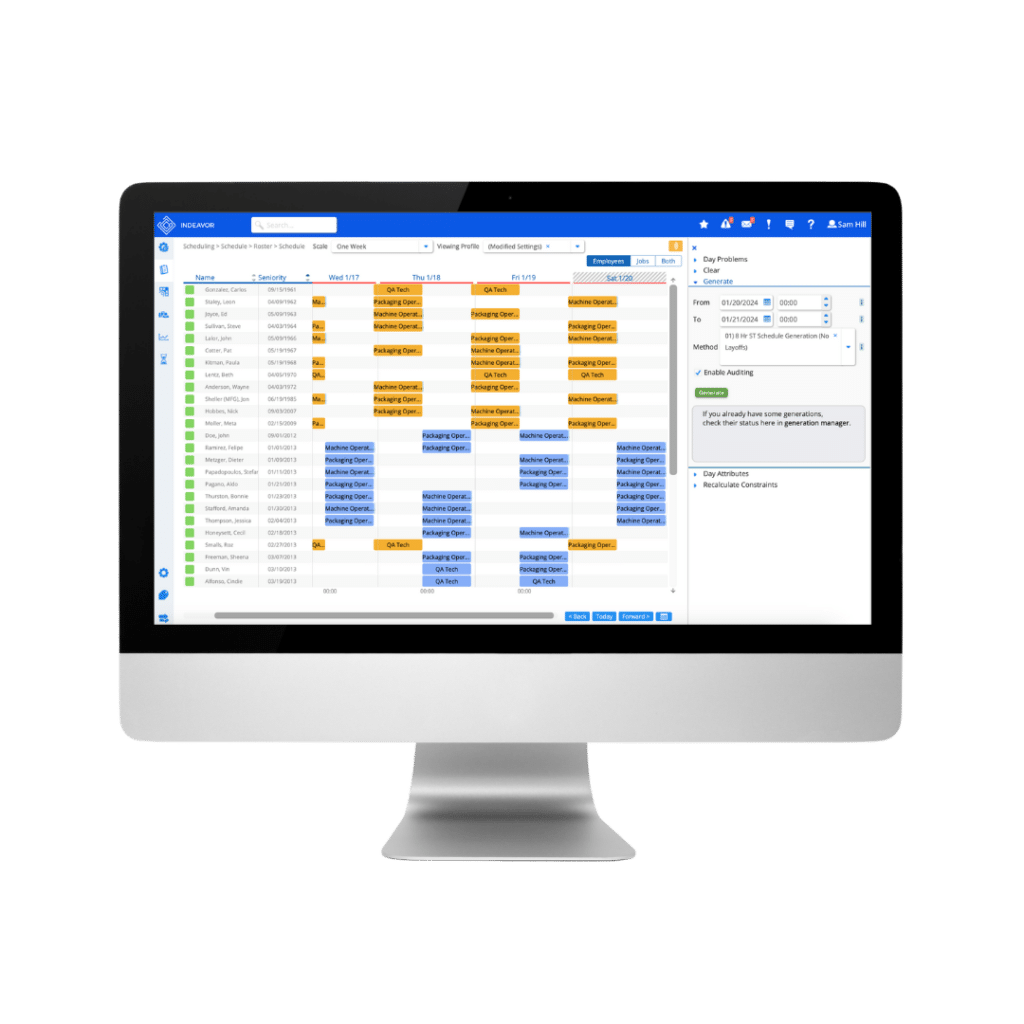
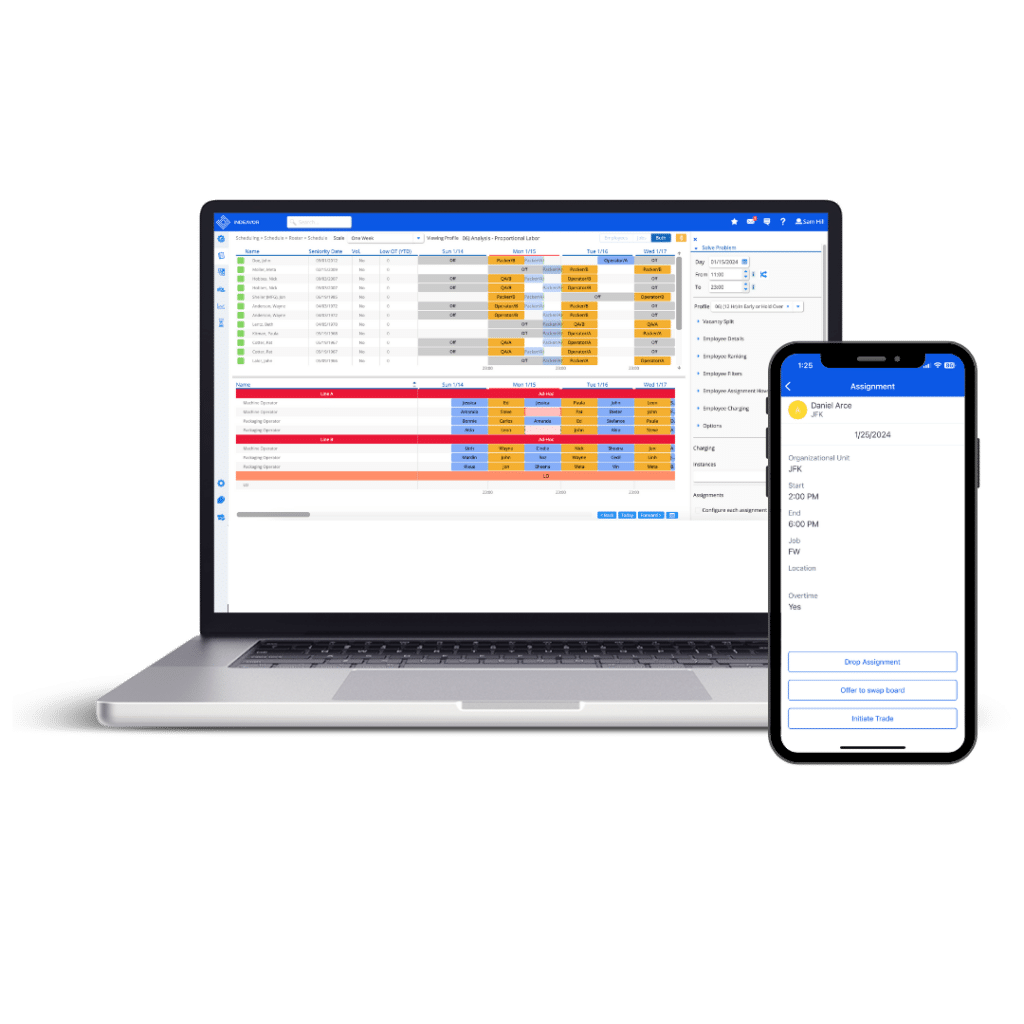
Optimized Scheduling
Effortlessly adjust to fluctuating labor and production with flexible scheduling that boosts efficiency, reduces waste, and ensures the right resources are allocated.
- Eliminate the need to access multiple systems and spreadsheets
- Make better in-the-moment decisions via a customizable interface that shows your organization’s most critical information
- Leverage automated straight time and overtime schedule generation
- Operate more efficiently by assigning the most qualified resources to changing demands via skills & competency management
Improve Frontline Worker Satisfaction
Enhance frontline worker satisfaction with flexible scheduling, fair overtime distribution, and easy access to shift swaps and time-off requests.
- Reduce Attrition by delivering schedule flexibility and smart shift swapping
- Reduce missed shifts and resulting punitive actions
- Provide access to overtime and ensure fairness in assignment
- Simplify access to time away from work
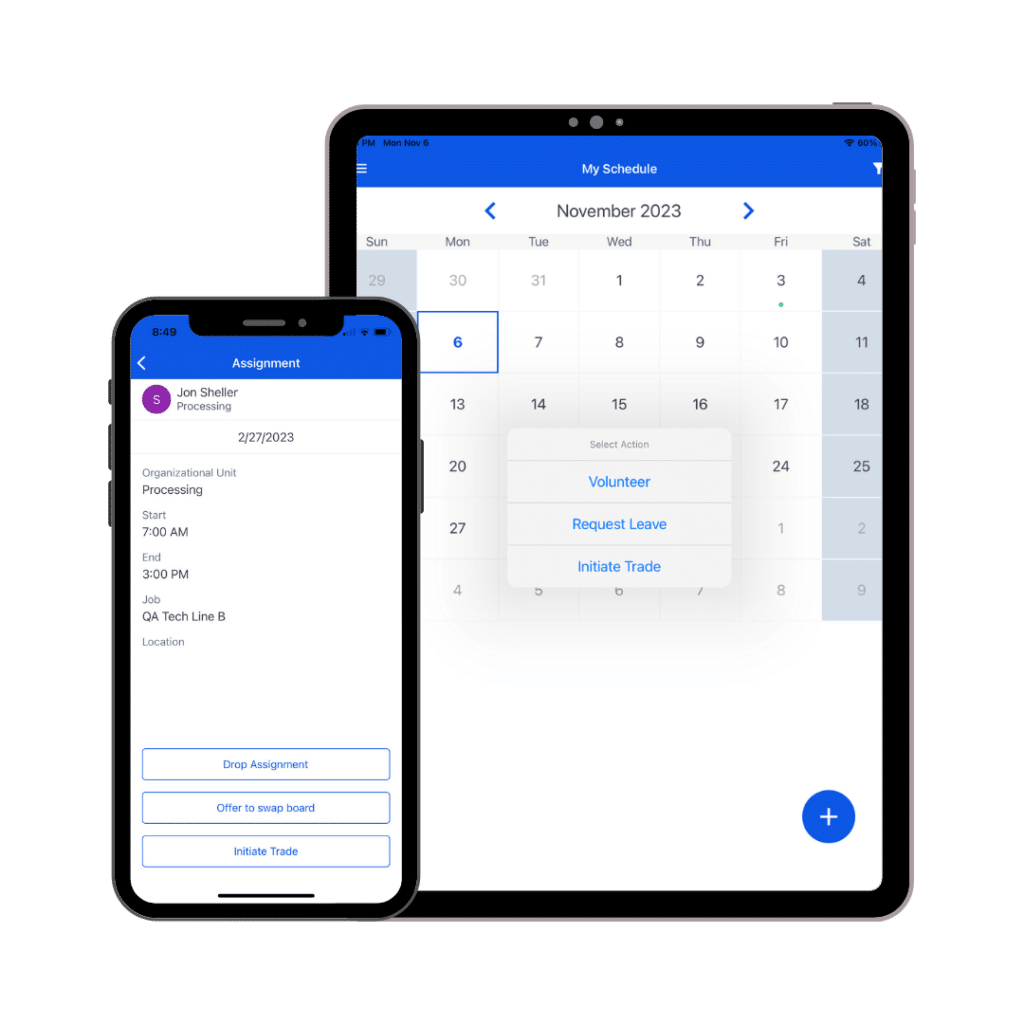
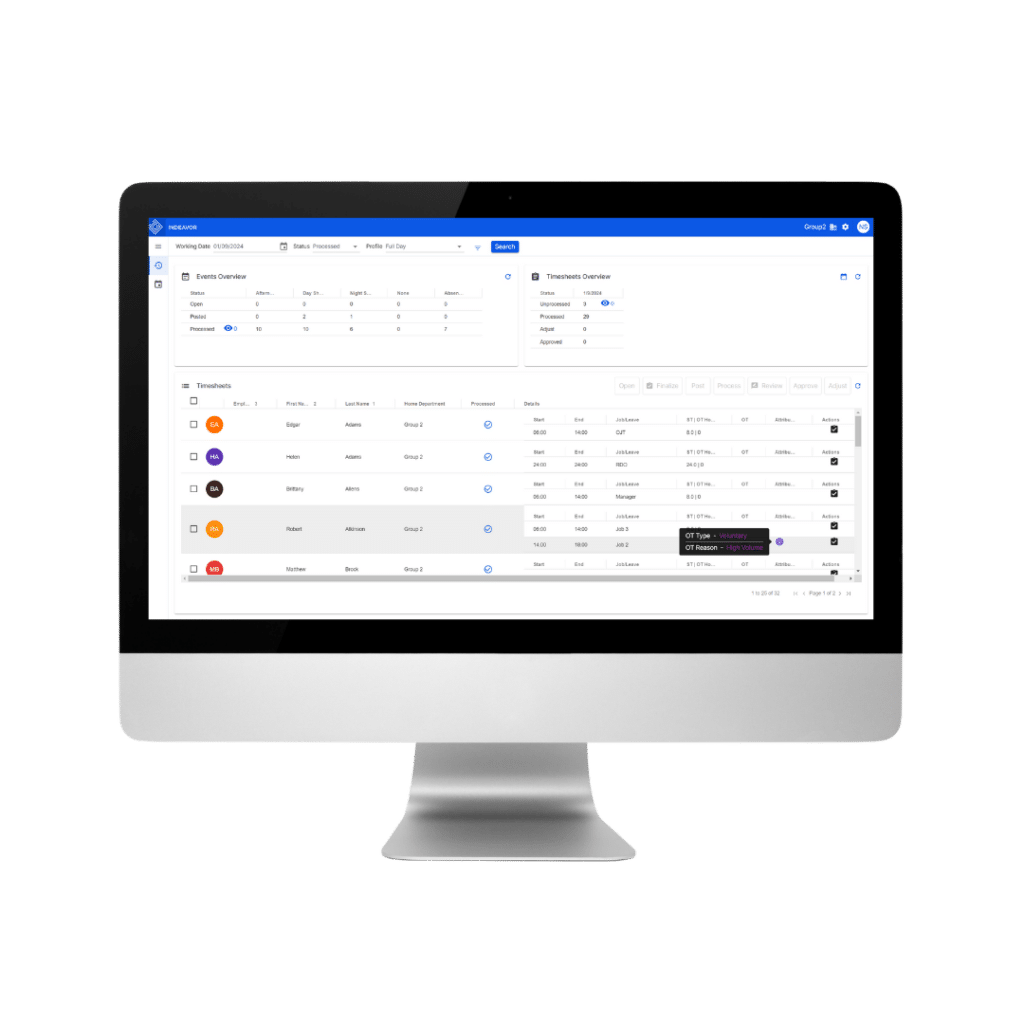
Enhance Compliance, Safety, and Quality
Strengthen compliance, safety, and quality with automated processes that ensure skilled worker placement and full transparency in scheduling decisions for peace of mind.
- Reduce safety risks through scheduling of properly skilled workers, proactively prevent workplace accidents
- Reduce grievances with automated Collective Bargaining Agreement (CBA) compliance
- Maintain audit trails of when, where, and who was scheduled and why changes were made
- Establish regular quality checks within the production schedule to ensure compliance and swiftly address any emerging issues
Data-Driven Decisions
Harness insights to optimize operations, enhance quality, and drive compliance across your organization.
- Leverage real-time data to quickly identify and address potential quality issues, reducing the likelihood of recalls
- Measure performance against scheduled labor, production standards, and SKUs
- Gain access to performance across networks of facilities, enabling better resource allocation and enhanced overall productivity
- Easily share data across your HRIS stack, helping streamline internal processes
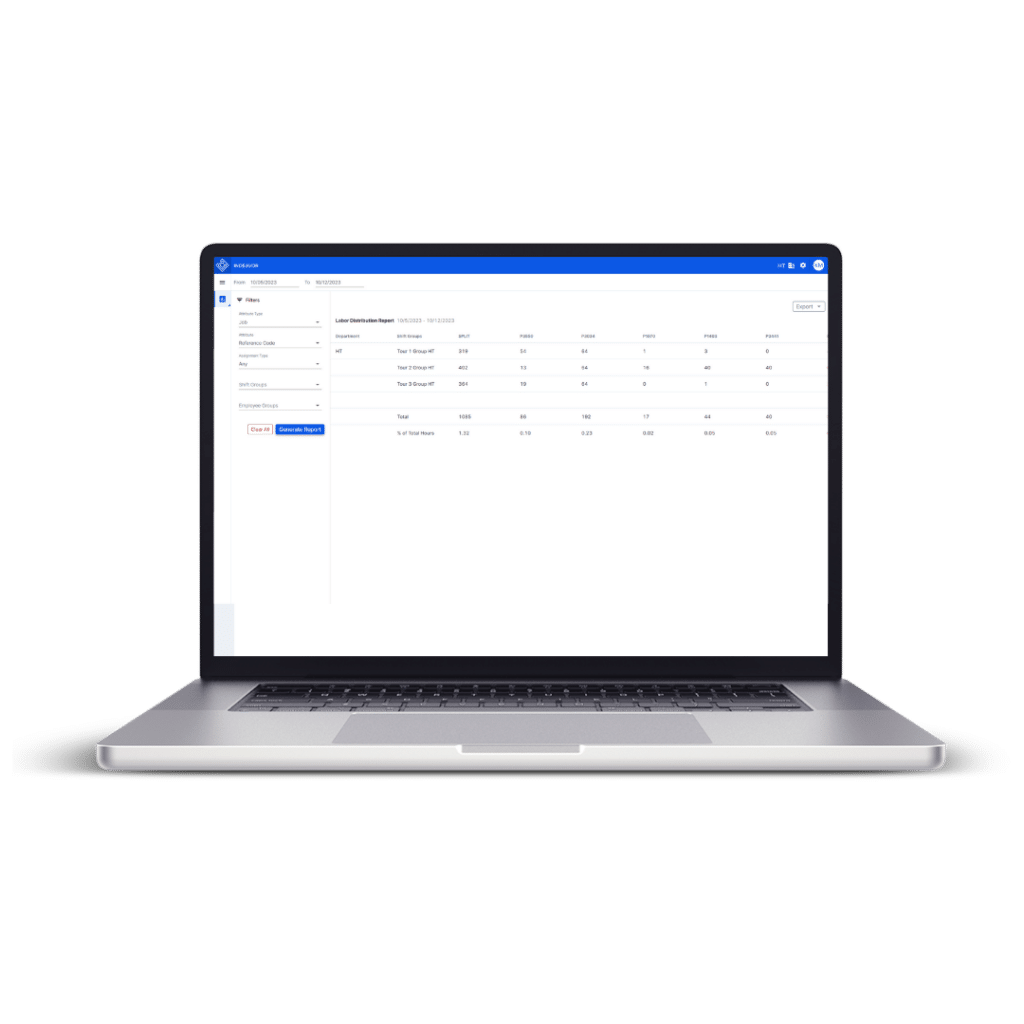
"Treehouse has been using Indeavor Engage for about 3 years and Indeavor call for 6 months. Indeavor Engage has been amazing for our employees and our supervisors. Engage has allowed our supervisors to post real time schedules and jobs for our employees and for our employees to be able to see their scheduled shifts for the work week... We are looking forward to integrating our systems to be able to continue eliminating our manual processes."
Frequently Asked Questions
Automated scheduling significantly reduces the time spent creating employee schedules and prevents under- or over-allocation of labor. This enables food processing facilities to respond quickly to production changes, maximize workforce utilization, and ultimately enhance profitability by eliminating unnecessary labor costs.
Analytics enhance workforce management in food processing by providing actionable insights that inform decision-making. By analyzing performance data against labor plans, food processors can identify inefficiencies, optimize labor allocation, and ensure the right resources are assigned to meet production demands. Access to performance metrics across multiple facilities allows organizations to benchmark productivity and share best practices.
Indeavor helps food processors maintain compliance through automated scheduling that ensures skilled workers are assigned to tasks, reducing safety risks and adhering to industry regulations. Our platform includes features for tracking compliance with collective bargaining agreements (CBA), maintaining detailed audit trails of scheduling decisions, and applying worker skills matrices during task assignments
Yes, Indeavor’s workforce management solutions can integrate with existing processes for waiver forms, fatigue assessments, and more, streamlining these activities for your business.
The platform saves time by automating fatigue rule calculations and reduces the risk of errors. It also saves money by eliminating excess labor costs from violation fines and unnecessary overtime.
Yes, you can book a live product demonstration with Indeavor to see how automated labor scheduling can improve workforce management for your business.
Learn More About Our Scheduling Software for the Food Processing Industry
Book a demo and our team of workforce management and labor optimization experts and we will customize an experience for your team.
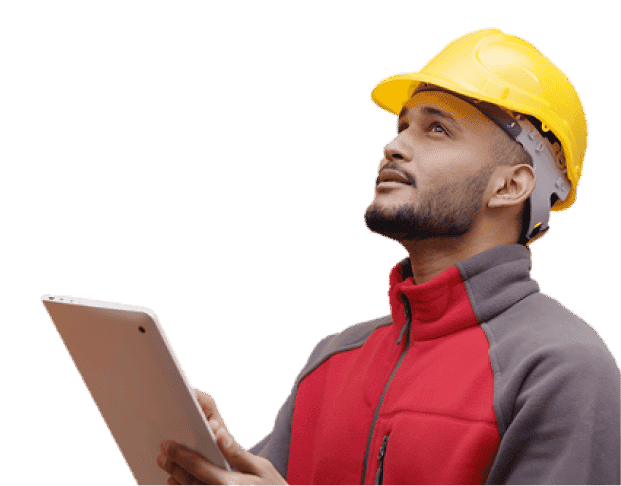