Traditional compliance methods often rely on manual documentation, audits, and inspections, which can be time-consuming, prone to errors, and lack real-time visibility into compliance status. When it comes to scheduling, relying on disparate processes (e.g., paper schedules, Excel spreadsheets, etc.) can be cumbersome and error-prone—particularly when a change occurs, such as a shift swap or sick employee—leading to inefficient allocation of resources, missed deadlines, and production delays. Similarly, ensuring each employee meets the necessary skills and competencies for each assigned job involves manual tracking of training records and certifications, which can be time-consuming and prone to oversight.
Technology can play a pivotal role in modernizing compliance processes by automating tasks, providing real-time insights, and enhancing overall efficiency and accuracy.
Significance of Compliance
Safety Regulations
Manufacturing environments often involve machinery, hazardous materials, and potentially risky operations. Compliance with safety regulations ensures the protection of workers from accidents, injuries, and occupational hazards. By adhering to safety protocols, manufacturers mitigate risks, promote a safe working environment, and safeguard the well-being of their employees.
Legal Compliance
The manufacturing sector is subject to various regulations and laws at local, national, and international levels. Adherence to laws and regulations regarding working hours, wages, and benefits is crucial for maintaining ethical and legal standards in workforce management. Compliance with these regulations is essential to avoid legal penalties, fines, or even shutdowns due to non-compliance—these fees can add up. According to a study conducted by the National Association of Manufacturers (NAM), regulations cost small manufacturers (<50 employees) over $50K per worker.
Quality Assurance
Compliance with quality standards and regulations is paramount in manufacturing to ensure that products meet predefined specifications and customer expectations. Non-compliance can result in defective products, recalls, and damage to brand reputation. By adhering to quality standards, manufacturers enhance product reliability, customer satisfaction, and market competitiveness.
Individual Site / Facility Standards
Adhering to workforce management regulations, such as scheduling and time off requirements, contributes to efficient operations within manufacturing facilities. Proper workforce planning, scheduling, and management help optimize resource utilization, minimize downtime, and maximize productivity. Compliance ensures that staffing levels align with production demands, helping to mitigate potentially dangerous employee burnout during peak times.
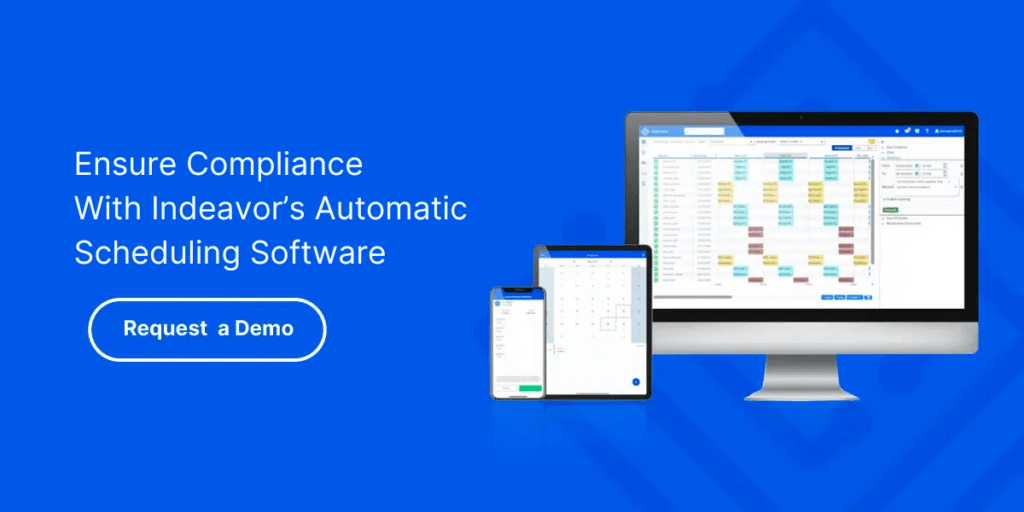
Challenges in Compliance Processes for Manufacturers
Complex Regulatory Landscape
Manufacturers must adhere to a myriad of regulations governing workforce scheduling, including maximum working hours, rest periods, and overtime limits. These regulations vary by region, further complicating the scheduling process. Ensuring compliance with these constraints requires meticulous planning and coordination to avoid violations and associated penalties.
Compliance also extends to ensuring that employees possess the necessary skills and competencies to perform their assigned tasks safely and effectively. This involves tracking certifications, qualifications, and training requirements, which can be challenging in industries with diverse skill sets and evolving job roles—especially when dealing with high turnover. According to a Forbes breakdown, the manufacturing industry has a 28.6% turnover rate, which is nearly 8x more than the national average of 3.6%, as indicated by the most recent Job Openings and Labor Turnover (JOLTS) report.
Manual and Paper-Based Processes
Many manufacturing firms still rely on manual and paper-based processes, leading to inefficiencies, an increased risk of errors, and compliance failures. Paper-based processes for managing workforce schedules are prone to errors, inconsistencies, and delays in updating schedules to reflect regulatory changes (e.g., a change in break laws) or unforeseen circumstances (e.g., unexpected employee absence).
Similarly, tracking employee skills, certifications, and training records manually can be cumbersome and error-prone. Maintaining accurate and up-to-date records becomes increasingly challenging as the workforce grows or undergoes changes.
Time-Consuming and Error-Prone Tasks
Compliance tasks such as data entry, record-keeping, and reporting are often labor-intensive and prone to human error, consuming valuable time and resources. Verifying compliance with scheduling constraints manually is a time-consuming process that involves cross-referencing schedules (sometimes which are out-of-date and not true to the realities of who was on the floor, and when). This manual effort increases the likelihood of errors and oversights, leading to non-compliance issues.
Tracking employee skills and competencies in places that are not centralized are not just inefficient, but can expose workers to safety threats when someone’s certification has unknowingly lapsed.
Lack of Visibility and Transparency
When manufacturers lack real-time visibility into shift schedules and employee hours, this makes it challenging for managers to identify scheduling conflicts, address issues with scheduling constraints promptly, and make informed decisions to optimize workforce utilization. Similarly, the lack of centralized systems for tracking employee skills and competencies hampers visibility and transparency in workforce management. Managers may struggle to access accurate and comprehensive data on employee qualifications, hindering effective workforce planning and development initiatives.
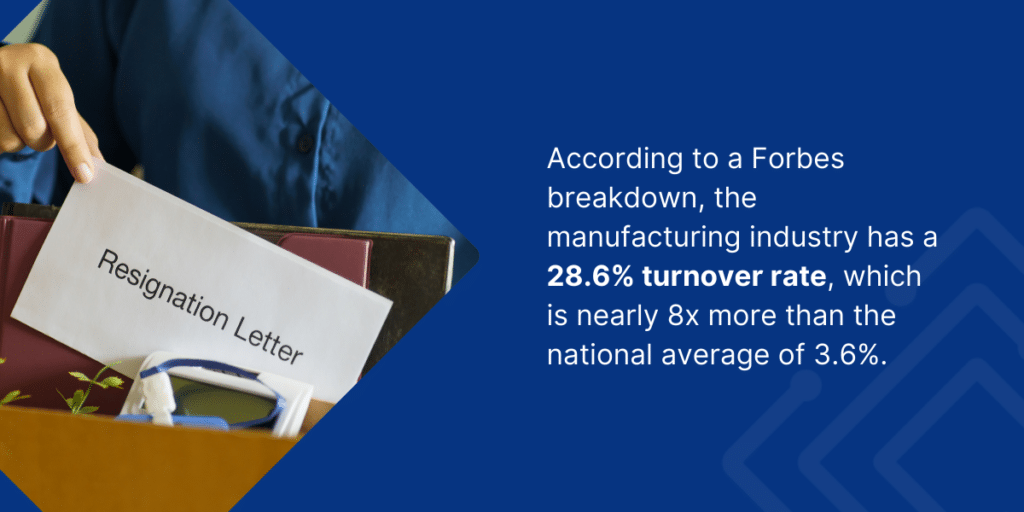
The Evolution of Technology in Compliance
In response to the challenges faced by manufacturers in keeping compliant, technology has undergone a significant evolution, revolutionizing the way compliance is managed and enforced. The introduction of basic software tools was designed to automate repetitive tasks, such as document management, record-keeping, and reporting. While these early digital solutions provided some efficiency gains over manual processes, they often lacked advanced capabilities and integration with other systems.
The emergence of Industry 4.0 technologies represented a significant advancement in the automation and digitization of compliance processes. Technologies such as the Internet of Things (IoT), robotics, and automation systems enabled manufacturers to collect real-time data from various sources across the production environment. This data could then be analyzed to optimize processes, identify compliance issues, and implement corrective actions proactively.
With the increasing volume and complexity of labor data generated by manufacturers, the integration of data analytics became essential for effective compliance management. Advanced analytics tools, including machine learning algorithms and predictive analytics models, allowed manufacturers to derive actionable insights from large datasets. These insights could be used to identify trends, patterns, and anomalies indicative of compliance risks or opportunities for improvement. By harnessing the power of data analytics, manufacturers could enhance decision-making, optimize processes, and achieve higher levels of compliance effectiveness.
Finally, the shift towards cloud-based platforms represented a fundamental change in how compliance solutions were deployed and managed. Cloud-based platforms offered manufacturers greater flexibility, scalability, and accessibility compared to traditional on-premises systems. Manufacturers could now access compliance tools and data from any location with an internet connection, facilitating collaboration and remote monitoring. Furthermore, cloud-based platforms provide enhanced security features, ensuring the integrity and confidentiality of compliance-related information. This shift towards cloud-based solutions empowered manufacturers to streamline compliance processes, reduce IT infrastructure costs, and adapt more quickly to changing regulatory requirements.
Benefits of Technological Integration in Compliance Processes
Improved Accuracy and Efficiency
The right technology improves the accuracy and efficiency of compliance processes by automating repetitive tasks, reducing manual errors, and streamlining workflows. Automated data entry, validation checks, and standardized processes ensure consistency and accuracy in compliance documentation. By minimizing human intervention and reliance on manual methods, technology helps manufacturers achieve higher levels of accuracy and efficiency in meeting regulatory requirements.
Technology allows for the automated creation and management of employee schedules based on predefined rules and constraints. This automation reduces the likelihood of scheduling errors, such as unbudgeted overtime or an uncertified employee being assigned to a particular job, ensuring that the right employees are assigned to the right tasks at the right times. Further, enabling the centralization of employee skill and competency data facilitates accurate tracking of certifications, training completion, and proficiency levels. Automated reminders and notifications ensure that employees stay up-to-date with required training, reducing the risk of non-compliance due to expired certifications or inadequate skills. This also helps with obeying regulations around company, local/state, and union rules.
Real-Time Monitoring and Reporting
One of the most significant benefits of technology integration in compliance processes is the ability to monitor and report compliance status in real-time. Advanced software solutions enable manufacturers to track key compliance metrics, such as workforce scheduling adherence, environmental performance, and product quality, in real-time. Real-time monitoring alerts stakeholders to potential compliance issues as they arise, allowing for prompt corrective actions and proactive risk management.
Being able to proactively abide by laws and regulations, see scheduling and overtime needs (and adjust weeks or months in advance), and even predict the amount of labor needed based on expected production demand provides a myriad of benefits. This includes ensuring that the organization maintains a competitive edge, optimizes resource allocation, and minimizes compliance-related risks, ultimately fostering operational efficiency and enhancing overall business performance.
Additionally, real-time reporting capabilities enable timely and accurate communication of compliance status to regulatory authorities, internal stakeholders, and external partners, enhancing transparency and accountability.
Solutions that allow for real-time monitoring of employee schedules and labor demand allow managers to track employee attendance, adherence to scheduled shifts, and compliance with labor laws and regulations. Any deviations from the planned schedule can be identified immediately, enabling managers to address issues promptly and adjust staffing as needed to maintain compliance. Real-time monitoring of employee skill and competency data provides visibility into workforce capabilities and gaps. Managers can quickly identify employees lacking the required skills or certifications for specific tasks, allowing for timely interventions such as additional training or reassignments to ensure compliance.
Enhanced Data Security and Compliance
Technology integration enhances data security and compliance by implementing robust security measures and ensuring adherence to data privacy regulations. Cloud-based compliance platforms offer advanced encryption, access controls, and audit trails to safeguard sensitive compliance-related information. In fact, when it comes down to assessing your potential vendors, it’s critical that they are SOC 2 compliant. Regular security updates and compliance certifications provide assurance that data handling practices meet industry standards and regulatory requirements. By centralizing data management and implementing stringent security protocols, technology helps manufacturers mitigate the risks of data breaches, unauthorized access, and non-compliance penalties.
Technology platforms offer secure storage and access controls for sensitive scheduling data, ensuring compliance with data privacy regulations. Encryption and authentication mechanisms protect employee information from unauthorized access or data breaches, safeguarding both privacy and compliance. Centralized skill and competency databases implemented on secure platforms ensure that employee training records and certifications are securely stored and managed. Access controls restrict access to authorized personnel only, preventing unauthorized modifications or tampering with compliance-related data.
Cost Savings and Resource Optimization
Technology integration in compliance processes leads to cost savings and resource optimization by reducing manual effort, minimizing errors, and improving labor sharing through skills management. Automated workflows and streamlined processes enable manufacturers to achieve greater productivity with fewer resources, resulting in cost efficiencies. Additionally, technology solutions facilitate better resource planning and utilization, ensuring that workforce, materials, and equipment are deployed effectively to meet compliance requirements. By eliminating inefficiencies and optimizing resource usage, technology integration helps manufacturers achieve significant cost savings over time, contributing to overall business sustainability and competitiveness.
Staying competitive is especially important given the current environment, where consumers are seeing high inflation in the consumer packaged goods (CPG) and food and beverage industries. Consumers are reacting by buying less, so CPG and food and beverage companies must be able to trim costs where they can.
Automated scheduling algorithms optimize workforce allocation based on demand forecasts, employee availability, and labor regulations. By efficiently matching labor supply with demand, technology minimizes overstaffing and overtime costs while ensuring compliance with labor laws governing working hours and breaks. Technology-driven workforce planning identifies skill gaps and training needs proactively, enabling targeted investments in employee development. By ensuring that employees possess the necessary skills and certifications for their roles, organizations reduce the risk of compliance violations and associated penalties while optimizing workforce productivity and performance.
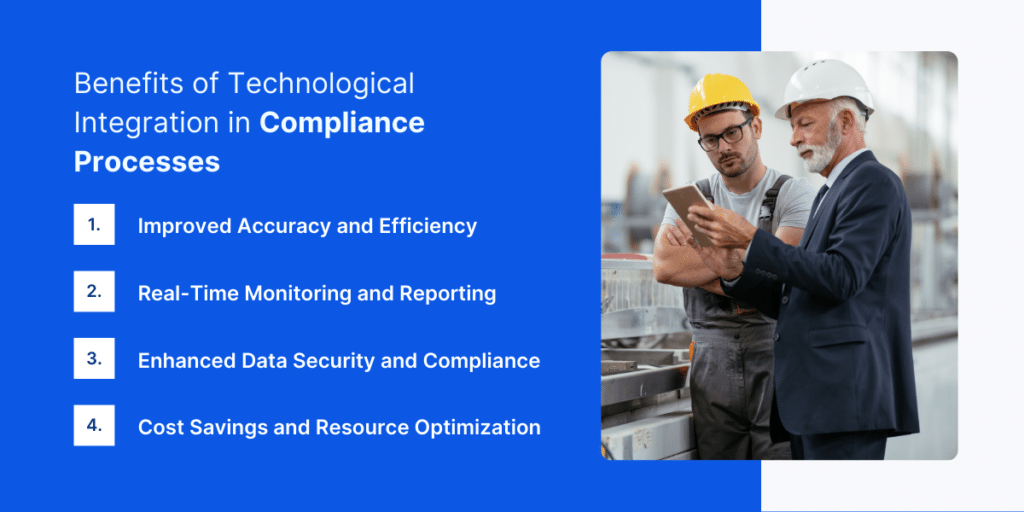
Best Practices for Implementing Technology in Compliance Processes
Conducting a Thorough Assessment of Compliance Needs
Manufacturers need to consider all of the below:
- Overtime allocation
- Scheduling constraints *
- Skills and competencies
- Environmental penalties
- Product recall avoidance
- Operational disruptions like downtime and production delays
* Predictive scheduling laws further complicate all this. Thus, manufacturers need a tool that automates, or otherwise streamlines, workforce management processes at manufacturing facilities—from scheduling employees to jobs through absence management and every disruption in between.
Before implementing a solution for labor scheduling, conduct a comprehensive assessment of compliance requirements, including labor laws, union agreements, and industry regulations. Identify specific scheduling constraints such as maximum working hours, rest periods, and overtime limits that need to be addressed at the point of scheduling. Can your potential solution ensure these constraints are adhered to when the roster is being made?
Assess your organization’s skill and competency requirements for each role and task. Identify regulatory requirements and industry standards for employee qualifications, certifications, and training. Determine the level of detail needed for tracking and reporting on skill compliance, including expiration dates and renewal cycles. The right solution will automate all this—or integrate with another solution that does. Speaking of integrations…
Selecting the Right Technology Partners and Solutions
Choose technology partners and solutions that offer robust scheduling features tailored to the manufacturing industry. Look for platforms that support flexible scheduling algorithms, compliance rule configuration, and, most importantly, integration with other systems that support key areas like:
- Employee Demographics: Real-time connection for employee information between HR systems and shift roster
- Production Demands: Direct alignment of labor requirements to production demands through ERP and demand planning integration
- Skills & Competencies: Ensure skill compliance and competency alignment for employee assignments
- Pay & Time Reconciliation: Real-time reconciliation of time and pay aligned to operating reality
- Business Intelligence: Advanced analytics with granular visibility to labor data
- Custom Automations: Leverage workflow automation to eliminate manual, tedious tasks
Employee Training and Change Management
Provide training to managers and supervisors on how to use the new manufacturing shift scheduling tool effectively. Communicate the benefits of the new system, including improved compliance, efficiency, and transparency. Address any concerns or resistance to change through clear communication and ongoing support.
Implement training programs to familiarize employees with the technology platform for tracking skills and competencies. Emphasize the importance of compliance with training requirements and the impact on job performance and career development. Encourage active participation and feedback from employees to foster buy-in and ownership of the compliance process.
Continuous Monitoring and Improvement
Establish regular audits and reviews of scheduling practices to ensure ongoing compliance with regulations and policies. Monitor key performance indicators such as overtime utilization, shift coverage, and adherence to scheduling constraints. Use feedback from stakeholders and performance metrics to identify areas for improvement and optimize scheduling processes.
Implement regular assessments of employee skills and competencies to identify gaps and training needs. Monitor compliance with training requirements and certification deadlines to prevent lapses or expirations. Continuously evaluate the effectiveness of the technology solution in meeting compliance objectives and make adjustments as needed.
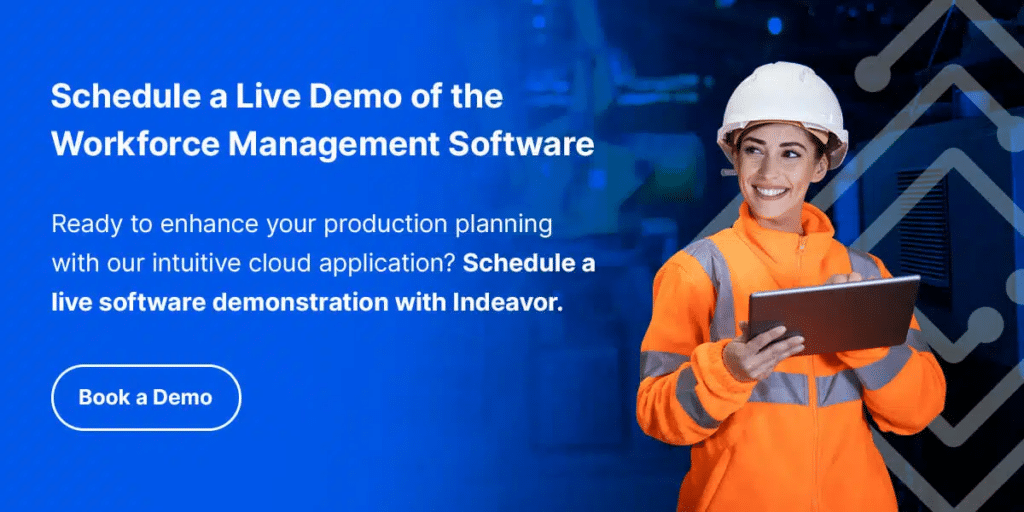
Embrace Technological Innovation
As discussed, using technology to streamline compliance processes offers a multitude of benefits, including improved accuracy and efficiency, real-time monitoring and reporting, enhanced data security and compliance, and cost savings and resource optimization. Manufacturers can streamline their compliance efforts, mitigate risks, and achieve greater operational excellence in today’s complex regulatory landscape. To explore the importance of replacing manual processes with tech overall, here are four ways going paperless can benefit your organization.
To prevent legal issues, penalties, and damage to reputation, organizations must prioritize compliance. Indeavor offers invaluable assistance in monitoring and enforcing compliance, mitigating the risk of human scheduling errors, and ensuring adherence to relevant laws and regulations. Through Indeavor’s workforce management solution for the manufacturing industry, compliance rules are seamlessly digitized and incorporated into our system. This allows for automatic evaluation of every action’s compliance status, streamlining the process and saving time and effort. By implementing proper guardrails within Indeavor, organizations can significantly reduce the effort required to verify compliance and ensure operations remain within legal boundaries.
Staying agile and adaptable is crucial for manufacturers facing evolving compliance requirements. Regulatory standards and industry guidelines frequently change, necessitating a proactive approach to compliance management. By remaining agile, manufacturers can swiftly adjust their processes, systems, and workforce training to meet new compliance demands. This agility ensures continued adherence to regulations, mitigates compliance risks, and maintains competitiveness in the dynamic manufacturing landscape.
Looking to optimize your manufacturing facilities? Book a demo today!