While both involve forecasting and planning to meet organizational objectives, labor demand planning and supply chain demand planning serve two distinct purposes. Let’s compare the two and learn why both processes are critical to long-term growth.
What is Labor Demand Planning?
Labor demand planning involves forecasting and managing the human resource needs of an organization (i.e., your employees). This includes determining how many and which type of employees are required to meet the organization’s production goals. Key aspects of labor demand planning include:
- Forecasting future labor needs based on factors such as production goals, market demand, technology changes, and employee turnover.
- Analyzing the skills and competencies required for various roles within the organization.
- Developing strategies for recruitment, training, and retention to ensure that the organization has the right talent in the right positions at the right time.
- Adjusting staffing levels in response to changes in business conditions, such as fluctuations in consumer demand or changes in strategic priorities.
What is Supply Chain Demand Planning?
Supply chain demand planning, on the other hand, focuses on forecasting and managing the demand for goods or materials. This includes predicting customer demand, coordinating production schedules, and optimizing inventory levels to meet customer needs efficiently. Key aspects of this process include:
- Forecasting customer demand—the prediction of what a company intends to sell—based on historical sales data, market trends, promotional activities, and other relevant factors.
- Collaborating with suppliers, production facilities, distribution centers, and retailers to ensure that the right products are available in the right quantities at the right locations.
- Balancing inventory levels to minimize stockouts while avoiding excess inventory carrying costs.
- Continuously monitoring and adjusting demand forecasts and production plans in response to changes in market conditions, customer preferences, or supply chain disruptions.
Differences at a Glance
- Focus: Labor demand planning focuses on managing all aspects of your workforce, while supply chain demand planning focuses on managing the flow and quantity of goods or materials.
- Inputs: Labor demand planning relies on factors such as production goals, consumer demand, and employee skills. Supply chain demand planning depends on factors like sales data, market trends, and inventory levels.
- Objectives: The objective of labor demand planning is to ensure that the organization has the right people with the right skills in the right positions to complete the required jobs/work orders. Meanwhile, the goal of supply chain demand planning is to ensure that products are available to customers when and where they are needed.
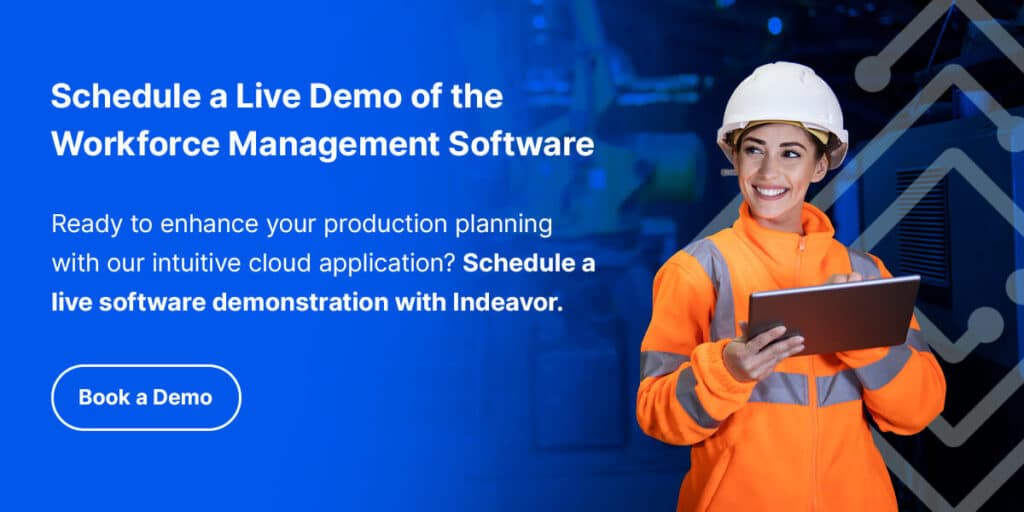
Why Both Processes Are Critical
Proper labor and supply chain demand planning contribute to sustainable growth and a competitive advantage. Here’s how:
Cost Optimization: By accurately forecasting demand for both labor and materials, companies can avoid unnecessary expenses associated with suboptimal staffing (e.g., over- or understaffing, grievances, overtime, etc.), excess inventory, or expedited shipments. This leads to improved profitability and overall better financial health.
Efficient Resource Allocation: By matching labor resources with production needs and ensuring the right amount of inventory is available at the right locations, organizations can minimize waste and idle capacity. This in turn contributes to more cost savings.
Enhanced Operational Efficiency: By streamlining processes, eliminating bottlenecks, and optimizing workflows, organizations can improve productivity, reduce lead times, and enhance overall operational performance. This translates into lower operating costs and increased competitiveness.
Responsive to Market Changes: By continuously monitoring market trends, demand patterns, and internal capabilities, companies can adjust staffing levels, production schedules, and inventory levels accordingly. This responsiveness helps minimize disruptions, avoid stockouts, and maintain high levels of customer satisfaction.
Strategic Alignment: By aligning workforce capacity with business goals and ensuring that supply chain activities support overall strategic objectives, companies can achieve greater synergy and coherence across different functional areas. This enhances agility and competitiveness in the marketplace.
Get the Best of Both Worlds With Indeavor
Indeavor is a workforce management solution purpose-built for the ever-changing needs of your manufacturing facility. With our labor demand planning capabilities, you can automatically match labor standards to production demands, ensuring shifts are never overstaffed or understaffed—during both planned and unplanned periods.
How does it work? To offer a truly end-to-end planning and execution platform, Indeavor integrates with supply chain demand planning solutions like OMP, SAP, or Oracle. Capabilities include:
- System of record for demand-based labor allocation standards
- Configurable, scenario-based workflows to accommodate manufacturing needs
- Purpose-built APIs for direct ERP and demand planning tools
- Production plan and horizon calculations based on SKU, asset type, or quantity
- Schedule automation accounts for changes in real time, ensuring seamless resource allocation
- Real-time notifications of schedule changes sent to employees and management
Without a unified workforce management solution, schedulers and front-line managers are saddled with planning day-to-day, every day. These people-dependent manual processes are done with little visibility, as there is no connection with one system of record for labor or materials demand.
Powered by Indeavor’s automated scheduling capabilities and straightforward ERP and supply chain planning integrations, manufacturers can instead enjoy:
- Planning weeks or months in advance
- System-driven automated processes supported by people-enabled changes
- Direct connection with the system of record (Indeavor) for labor and materials demand