Modern systems allow businesses to make nearly every decision based on data. Scheduling is no exception.
By using historical information to create schedules, companies can mitigate common challenges, such as labor demands and product shortages. Schedule forecasting can analyze countless data points from your company’s historical performance and analyze them to create a plan that’s as efficient and effective as possible.
What Is Schedule Forecasting?
Schedule forecasting in workforce management is the process of predicting and planning for future staffing needs within an organization. It involves using historical data, analysis, and various forecasting techniques to create schedules that align with the expected demand for labor resources. The primary goal of schedule forecasting is to ensure an organization has the right number of employees with the necessary skills to meet customer demand while also controlling labor costs and optimizing productivity.
This process is a critical component of workforce management, particularly in industries with fluctuating demand, such as manufacturing, food processing, oil and gas, and the public sector. By accurately predicting and planning for labor needs, organizations can enhance operational efficiency, control costs, and improve customer service, all while ensuring a better work environment for employees.
The Significance of Historical Data
Historical data forms the basis for most forecasting systems. Whether you’re assessing finances, labor, or another point, everything depends on information collected during prior business operations. Examples of components you might collect for scheduling include call-outs, production quotas, and available team member qualifications. You can also review data from outside your organization, like consumer trends and cost indexes.
With these details, schedule forecasting software can start to identify trends and patterns. Accuracy at this stage is critical since it will feed into analysis and eventual insights. A lack of dependable data can render those insights useless. In comparison, high-quality historical data allows businesses to anticipate fluctuations in demand and plan with a high degree of confidence.
Fortunately, many manufacturers have enormous amounts of data at their disposal. The challenge lies in putting it to work. Humans simply can’t work with the vast number of data points available, so historical data forecasting tools are necessary to make sense of it all.
Labor Analytics: Unveiling Insights
You can enlist labor analytics to make the most of historical data. This approach employs analytics software to identify staffing needs for meeting operational demands.
For example, you might use labor analytics to determine if you have the right staff scheduled for a shift. Say you get a sudden rush order on the manufacturing floor. Labor analytics can review the demands and help you identify the best employees for upcoming shifts, considering factors like qualifications and job roles.
Modern businesses use labor analytics to make data-driven decisions. It uses objective, historical information on staffing and labor demands to support the most effective choice for a given scenario. Labor analytics is especially valuable in responding to interruptions quickly and setting yourself up for flexibility with proactive planning.
Labor analytics tools can provide visibility into scheduling demands and efficiency, and they’re an excellent component to have in your labor management program. Your labor analytics system can then integrate with other aspects of labor management, from your enterprise resource planning solution to payroll.
However you plan to use it, your labor analytics system should offer actionable insights that point you in the right direction. Some tasks that labor analytics tools can help with include:
- Preparing for and responding to demand fluctuations in real time.
- Eliminating guesswork during scheduling.
- Optimize staffing levels for cost-effective yet efficient operation.
- Visualize labor scheduling matched to production schedules.
By linking your operations and labor, an analytics program can dramatically improve staffing levels and responsiveness for an optimized workflow.
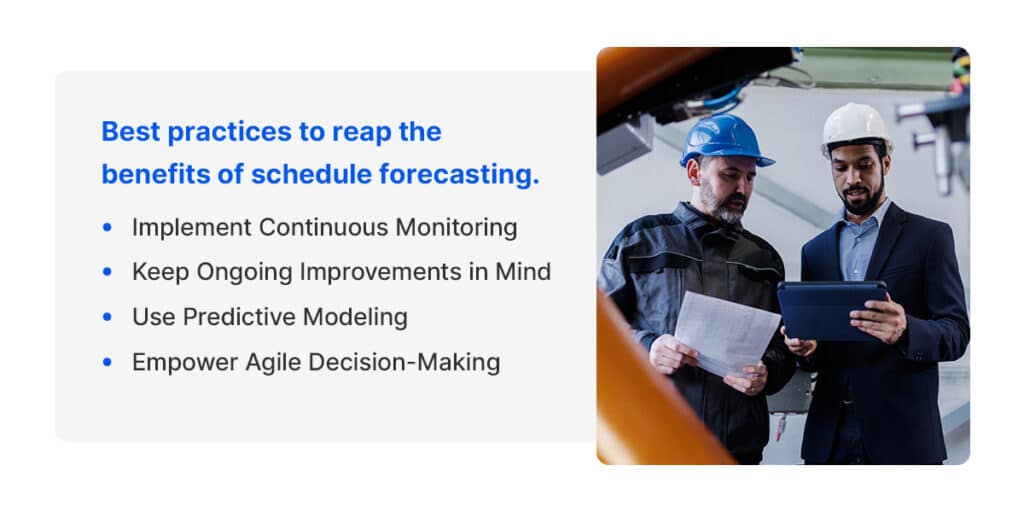
Adapting to Uncertain Times: Best Practices
Even with these modern resources, the available labor can be unpredictable. Whether they work in manufacturing, food processing, oil and gas, or another production setting, users must implement some best practices to reap the benefits of schedule forecasting.
Implement Continuous Monitoring
With so much technology at work, industrial businesses have a unique opportunity to monitor virtually everything that happens in the facility at any time. Embracing the Internet of Things can help you get a real-time view of your production line, improving the quality of your data and enabling you to make decisions based on the most recent information.
Continuous monitoring applies to more than just what happens on the floor. You’ll also want to stay up to date on information related to your team members. Stay current with data points such as employee qualifications, overtime status, and fatigue compliance rules. Consider implementing a Continuous Planning approach to improve your response to changes.
Keep Ongoing Improvements in Mind
Simply implementing advanced schedule forecasting software isn’t enough. You’ll need an adaptive program and mindset to support continual growth. The industry will continue to innovate, and you might lose your competitive advantage if you don’t keep up. A flexible approach to scheduling and access to the latest data can help you adapt to industry changes and stay ahead of the curve.
Use Predictive Modeling
Predictive modeling allows you to predict future behavior using statistics related to your historical data. This feature is a powerful tool for production environments, which can change quickly. When interruptions appear, such as a supply chain issue or a spike in demand, you can be ready with quick predictions that help you minimize costs or downtime.
For example, if previous years show that team members are more likely to call out during flu season, a predictive model might see that coming. With some warning, you can take steps to mitigate the issue, like hiring a few additional part-timers to pick up the shifts.
Empower Agile Decision-Making
Sometimes, you need to make decisions quickly, but that doesn’t mean you need to forego data analysis. Make sure your production scheduling solution can provide up-to-date information in an actionable format. Decision-makers can then view the data quickly and respond with confidence, no matter how unpredictable the situation is.
The Future of Labor Scheduling
As with most technological fields, schedule forecasting is evolving quickly. We can expect artificial intelligence to play a significant role in future capabilities, along with machine learning and predictive algorithms. These algorithms may start to incorporate more advanced data points and juggle different priorities.
Automation is another big player in business forecasting solutions. Minimizing human involvement is crucial for maximizing efficiency and reducing errors. Enabling automation, especially in response to changing conditions, can help scheduling run smoothly and reduce requirements for administrative teams.
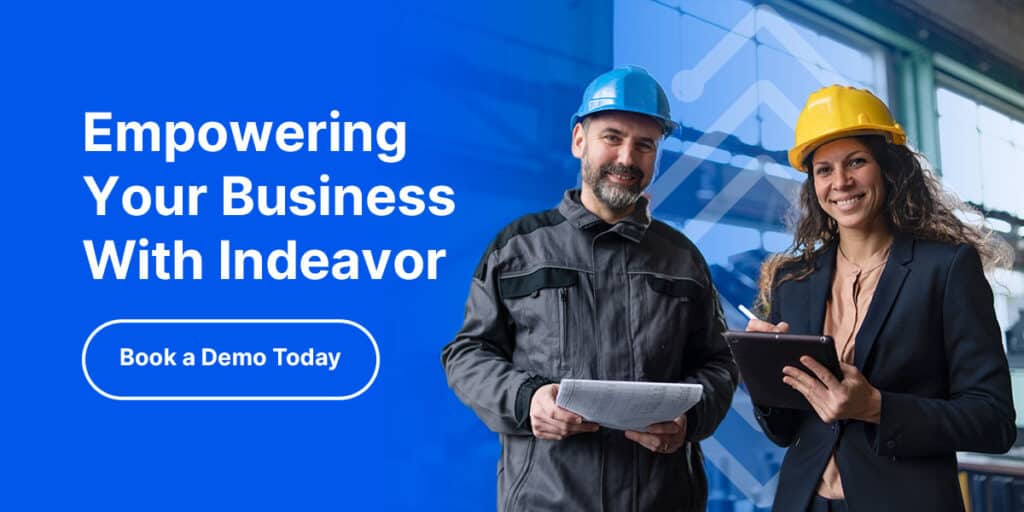
Empowering Your Business With Indeavor
Historical data and labor analytics play a pivotal role in improving scheduling. If you want to work as efficiently and effectively as possible, start by implementing the right tools.
Indeavor’s workforce management software is optimized for the complexities of industrial environments and their unpredictable nature. Our system puts historical data and production analytics at the forefront with features like demand-driven employee scheduling, real-time workforce visibility, and actionable insights for better decision-making. Pair your historical data with our user-friendly interface and real-time management tools to upgrade your schedule forecasting.
Book a demo today to learn more about the Indeavor solution and how we can put your data to work.