Reasons For Shortages in the Food Processing Industry
There are a few key reasons why the food processing industry is experiencing a labor shortage:
- Aging workforce: Many experienced workers are reaching retirement age, creating a gap in skilled labor. The industry must attract and train new workers to address this workforce transition.
- Limited awareness and perception: Many individuals may need to be aware of the diverse career opportunities available within the industry or may have misconceptions about the nature of work in food processing.
- Workforce migration: As economies evolve, workers may migrate to other sectors that are perceived to offer better wages, working conditions, or career prospects. This migration of skilled workers reduces the available talent pool for the food processing industry, making it harder to fill vacancies and meet industry demands.
- Changing work-life balance expectations: Modern workers increasingly prioritize work-life balance and seek jobs that offer flexibility and personal fulfillment. However, the nature of work in the food processing industry, which often involves shift work, physical labor, and fast-paced environments, may not align with these expectations.
- Impact of global events: Global events, such as economic recessions, pandemics, or natural disasters, can have a significant effect on labor availability. These events can disrupt supply chains, affect workforce mobility and create uncertainty in the job market. For example, the COVID-19 pandemic highlighted the vulnerabilities of the food processing industry and led to workforce disruptions, further exacerbating labor shortages.
- Skills mismatch: Technological advancements and evolving industry practices require workers with specialized knowledge and skills. However, there may be a gap in the skills possessed by job seekers, leading to difficulties in finding qualified candidates for specific roles within the industry.
Strategies to Overcome Labor Shortages
To address the food processing labor shortage in the industry, companies must employ strategies that encompass both short-term and long-term solutions. By implementing the following approaches, employers can navigate the challenges and ensure a steady supply of skilled workers.
Improving the Perception of Food Processing Jobs
To deal with labor shortages and attract talent, businesses must enhance the perception of food processing jobs. Highlight the benefits and opportunities within the industry, such as competitive wages, career advancement, and skill development. Emphasize the diverse range of roles and the potential for growth and innovation.
Companies can attract a broader talent pool by showcasing opportunities and benefits:
- Highlighting benefits and opportunities: Benefits include competitive wages, comprehensive benefits packages, and opportunities for advancement. Emphasize the stability and growth potential of the industry and showcase the diverse range of roles available, from production line workers to quality control specialists and logistics managers.
- Showcase skills development and career growth: Highlight employee training programs, certifications, and skill-building opportunities. Demonstrate success stories of individuals who have advanced their careers within the food processing sector.
- Promoting workplace safety and hygiene: Emphasize strict adherence to safety protocols, cleanliness standards, and quality control measures within the industry. Highlight investments in state-of-the-art equipment and technologies contributing to a safe and hygienic working environment.
- Leveraging digital platforms: Utilize online and social media channels to show the positive aspects of food processing jobs. Share success stories, employee testimonials and behind-the-scenes glimpses of the work environment. Engage with potential candidates through targeted digital marketing campaigns to raise awareness about the industry and its career opportunities.
The manufacturing industry has long been grappling with labor shortages. The food and beverage industry is no exception to this trend. While the COVID-19 pandemic exacerbated the situation with the surge in grocery demand, the need for workers ranging from processing and packaging machine operators to plant supervisors, managers, and even data scientists has steadily increased for over a decade.
Companies have made numerous efforts to attract and retain the necessary workforce to meet market demands. However, there is no simple solution to make the labor shortage problem disappear, especially with the current unemployment rate at 3.7%. A study from Deloitte and The Manufacturing Institute estimates that United States manufacturers will have 2.1 million open jobs by 2030.
Nevertheless, companies can adopt a multifaceted approach to close existing talent gaps and position themselves favorably for the future. Success will hinge on adopting a “yes and” approach, implementing a range of initiatives that ultimately lead to a comprehensive transformation in talent sourcing and retention strategies to combat labor shortage in the food industry.
Strengthening Workforce Training and Development
A key strategy to overcome labor shortages in the food processing industry is prioritizing workforce training and development. Strategies should focus on attracting and training new talent and adapting to the evolving expectations of the modern food production labor workforce. Here are some approaches to strengthening workforce training and development:
- Collaboration with educational institutions: Establish partnerships with academic institutions, such as community colleges, vocational schools, and technical institutes. Develop industry-relevant curriculum and training programs, like certificate programs, apprenticeships, or customized courses tailored to the food processing industry.
- On-the-job training and mentorship: Implement comprehensive on-the-job training programs for new hires and existing employees. Provide structured training that covers essential job skills, safety procedures, and standard operating practices. Assign experienced employees as mentors to guide and support new hires during their initial training period.
- Continuous skill development: Encourage employees to develop and learn continuously. Offer opportunities for employees to attend workshops, seminars, or industry conferences to stay updated with the latest trends, technologies, and best practices in food processing. Provide access to online learning platforms or support employees pursuing relevant certifications or higher education in fields related to food processing.
- Cross-training and multi-skilling: Promote cross-training initiatives to enable employees to acquire diverse skills within the food processing industry. Encourage employees to learn different roles and tasks, allowing for flexibility and adaptability in workforce management.
- Recognition and reward programs: Implement recognition and reward programs to acknowledge employees’ efforts and achievements in training and skill development. Recognizing and rewarding employees’ commitment to improving their skills creates a positive culture of learning and development within the organization.
- Knowledge sharing and internal training resources: Encourage internal training sessions, where experienced employees can conduct training sessions or workshops on specific topics. This approach enhances the workforce’s skills and creates a collaborative and supportive environment that facilitates continuous learning.
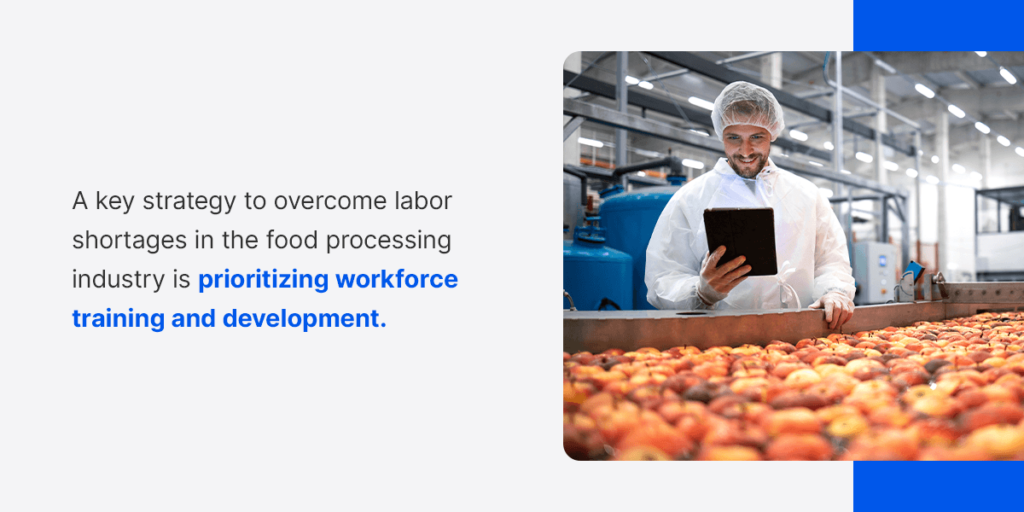
Enhancing Recruitment and Retention Efforts
Companies must focus on attracting new talent and retaining existing employees to address labor shortages in the food processing industry. By implementing effective recruitment and retention strategies, organizations can build a strong workforce and mitigate the challenges posed by labor shortages:
- Targeted recruitment strategies: Implement targeted recruitment strategies to attract talent, including online job postings, partnerships with local employment agencies, and participation in job fairs and industry events. Craft compelling job descriptions highlighting the benefits and opportunities within the food processing industry.
- Competitive compensation and benefits: Conduct market research to ensure your wages and benefits align with industry standards. Consider additional perks such as health care benefits, retirement plans, and flexible work arrangements.
- Workplace safety and employee well-being: Implement and enforce strict safety protocols to minimize accidents and injuries. Conduct regular training sessions to educate employees on safety practices. Additionally, consider initiatives that promote employee well-being, such as wellness programs, employee assistance programs, and work-life balance policies.
- Professional development and growth opportunities: Provide employees with training programs, workshops, and seminars to enhance their skills and knowledge. Implement clear career development pathways and offer opportunities for promotions and advancement.
- Positive company culture and employee engagement: Encourage employee engagement through regular team-building activities, social events, feedback, and idea-sharing opportunities. Recognize and reward outstanding performance to boost morale and create a sense of appreciation.
- Employee referral programs: Incentivize employees to refer qualified candidates by offering referral bonuses or other rewards.
Leveraging Technology and Automation
Explore automation solutions for repetitive and labor-intensive tasks, allowing employees to focus on higher-value responsibilities. Here are some key aspects to consider when leveraging technology and automation:
- Robotic systems: Implement robotic systems to automate repetitive and physically demanding tasks in food processing operations. Technicians can program robots to perform tasks such as sorting, cutting, packaging, and palletizing, reducing the need for manual labor.
- Automated sorting and inspection: Optical scanners, sensors, and machine vision technologies can detect defects, foreign objects, and quality issues in food products. Automated systems can sort and reject faulty products, reducing the need for manual inspection and improving overall product consistency and safety.
- Internet of Things (IoT) and data analytics: Leverage IoT devices and sensors to gather real-time data on food processing operations. Predictive maintenance can be implemented to proactively identify potential equipment failures, reducing downtime, and improving operational efficiency.
- Process optimization and workflow automation: Analyze existing workflows and identify areas where automation can improve efficiency. Automate ingredient mixing, temperature control, cooking, and packaging processes to streamline operations and reduce manual labor requirements. Implement software solutions that enable real-time monitoring and control of production processes, ensuring consistency and minimizing errors.
- Collaborative robots (Cobots): Cobots are designed to assist and collaborate with humans, performing tasks that require dexterity and flexibility. They can enhance productivity, improve ergonomics and help bridge the skills gap by complementing human capabilities in complex tasks.
- Training and upskilling employees: As technology and automation systems are implemented, provide training and upskilling opportunities to employees. Training programs can focus on programming, operating, and troubleshooting automated systems, enabling employees to adapt to changing job requirements.
- Continuous technological innovation: Collaborate with technology providers, research institutions, and industry associations to explore emerging technologies that address specific labor challenges. Regularly evaluate and upgrade existing automation systems to utilize the latest innovations.
Collaboration With Government and Industry Partners
Companies can address systemic challenges and create a supportive environment that fosters the availability of skilled workers with these actions:
- Workforce development programs: Work with government agencies and industry associations to develop workforce development programs that align with the needs of the food processing industry. Advocate for funding and support for training initiatives, apprenticeship programs, and vocational education.
- Policy advocacy: Engage in advocacy efforts to shape policies that support the food processing industry’s workforce needs. Work with industry associations to voice concerns and propose recommendations to government entities.
- Industry-driven training initiatives: Work with industry partners to develop industry-driven training initiatives. Collaborate on designing and delivering training programs that address specific skill gaps in the food processing industry. Pool resources and expertise to create comprehensive training modules encompassing technical skills, safety practices, and industry-specific knowledge.
- Sharing labor market data: Collaborate with government agencies and industry partners to share labor market data and insights. Companies can better align their recruitment and training strategies by sharing information on current and projected workforce needs.
Investing in Employee Well-Being and Work-Life Balance
Employers must recognize the importance of investing in employee well-being and promoting a healthy work-life balance to overcome labor shortages in the food processing industry. Here are some strategies for investing in employee well-being and work-life balance:
- Flexible work arrangements: Offer flexible work options such as flexible schedules, remote work, or compressed work weeks. These arrangements allow employees to manage their personal obligations better and achieve a healthier work-life balance.
- Wellness programs: Offer access to gym facilities, fitness classes, or wellness workshops. Provide resources for stress management, healthy eating, and mental health support.
- Clear communication and expectations: Foster open and transparent communication channels to ensure employees have clear expectations, job responsibilities, and work schedules. Clearly define roles and responsibilities and provide realistic timelines for completing tasks.
- Encouraging breaks and time off: Promote a culture that values rest, acknowledging the importance of recharging and rejuvenating.
- Supportive work environment: Cultivate a supportive and inclusive environment that values diversity, respects work-life boundaries, and promotes teamwork. A supportive work environment fosters employees’ sense of belonging, well-being, and loyalty.
Embracing Sustainable Practices
By incorporating sustainable practices into their operations, food processing companies can contribute to a greener future, enhance their reputation, attract eco-conscious customers, and appeal to prospective employees passionate about sustainability. Consider the following strategies for sustainable practices in the food processing industry:
- Sustainable sourcing: Prioritize the use of sustainably sourced ingredients and raw materials. Partner with suppliers who adhere to sustainable farming practices, support fair trade initiatives, and promote responsible resource management.
- Waste reduction and recycling: Explore ways to minimize food waste through improved production planning, inventory management, and product development. Implement recycling initiatives for packaging materials, such as plastics, cardboard, and metals, to minimize the environmental footprint and contribute to a circular economy.
- Energy and water efficiency: Implement energy-efficient technologies and practices to reduce energy consumption and carbon emissions. Prioritize water conservation measures, such as water-efficient equipment and systems, and raise awareness among employees about the importance of water stewardship.
- Packaging innovation: Explore sustainable packaging alternatives to reduce the environmental impact of packaging materials. Consider using biodegradable, compostable, or recycled packaging materials. Encourage customers to recycle or return packaging for reuse.
- Supply chain collaboration: Collaborate with suppliers, logistics partners, and stakeholders to drive sustainability across the entire supply chain. Engage in dialogues and initiatives to reduce greenhouse gas emissions, promote sustainable transportation practices and minimize environmental impacts of transportation and distribution.
- Carbon footprint reduction: Develop strategies to measure and reduce the carbon footprint of food processing operations. Becoming sustainable may involve implementing energy-efficient practices, utilizing renewable energy sources, and exploring opportunities for offsetting carbon emissions.
- Community engagement and social responsibility: Engage with local communities and support social responsibility initiatives. Partner with local organizations, donate excess food to food banks or charitable organizations and contribute to community development projects.
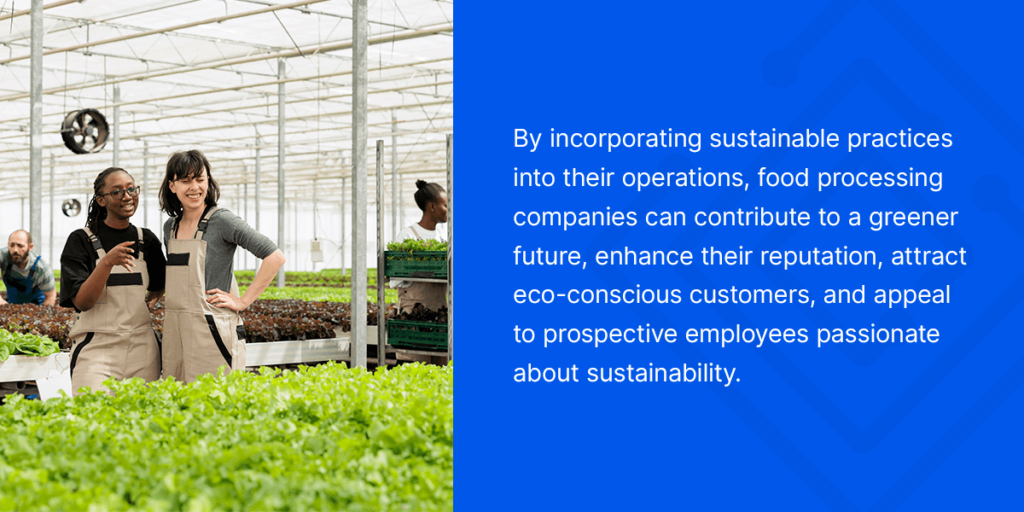
Utilizing People-First Automation With Indeavor
In the face of labor shortages and the need for efficient workforce management in the food processing industry, Indeavor offers a solution prioritizing people and automation. With manual processes often leading to human errors, compliance challenges, and difficulty tracking labor data, Indeavor’s cloud-based software provides a comprehensive solution.
By leveraging their demand planning capabilities and automated scheduling features, Indeavor helps organizations ensure that qualified employees are assigned to each job, even in last-minute vacancies, mitigating compliance risks. Their customizable interface presents critical information in real-time, enabling better decision-making, while centralized data and auto-logged records ensure compliance with regulations like the FDA’s Food Safety Modernization Act (FSMA).
Indeavor’s software streamlines labor management by providing transparent and easily accessible scheduling information. It eliminates the distribution of unnecessary overtime by accurately tracking employee requests and hours worked.
With skills certification and availability-based scheduling features, Indeavor helps fill sudden scheduling gaps with qualified workers, ensuring productivity and compliance. Furthermore, their system automatically tracks qualifications, sends renewal notifications, and maintains an audit trail of who worked on what machine during each shift, providing the necessary documentation for regulatory compliance.
By adopting Indeavor’s people-first automation, the food processing industry can optimize labor resources, mitigate compliance risks, and improve operational efficiency. Their team of workforce management and labor optimization experts can provide customized solutions tailored to each organization’s specific needs. Through Indeavor’s software, companies can take control of shift schedule automation and ensure a productive and compliant workforce.
The food processing industry’s labor shortages and compliance challenges can be addressed effectively through Indeavor’s people-first automation. Using their cloud-based software, companies can streamline scheduling, track labor data accurately, and assign qualified workers to each position. With Indeavor’s focus on people and automation, the industry can navigate labor shortages while maintaining high compliance standards, productivity, and employee satisfaction.
Book a demo with Indeavor’s experts to experience the benefits firsthand and revolutionize your workforce management practices.