In the ever-evolving landscape of Manufacturing and Energy markets, staying ahead of the curve is not just an aspiration but a necessity. Industry 4.0 fast-paced transformation involves the integration of digital technologies, real-time data analytics, advanced robotics, cyber-physical systems, and many other Smart Manufacturing concepts. This transformation is accompanied by a natural evolution of operational systems.
World Class Manufacturing (WCM) is emerging as the successor to Total Productive Maintenance (TPM), Lean Six-Sigma methodologies are reshaping the foundations laid by classic Six-Sigma, and with the power of digitalization and system integration, it becomes crucial for enterprises to align their Operational Excellence strategies with these advancements.
Evolution from TPM to WCM
Traditionally, TPM has been a cornerstone in achieving operational excellence, focusing on maximizing equipment efficiency and minimizing downtime. However, with the emergence of WCM, organizations are adopting a more comprehensive approach that extends beyond maintenance.
WCM integrates TPM principles but expands its scope to encompass the entire production system, emphasizing excellence in all aspects of manufacturing. This transition signifies a paradigm shift towards a more holistic approach to manufacturing, integrating various methodologies, focusing not only on maintenance but on the entire production process, fostering a culture of continuous improvement and efficiency.
TPM culture emphasizes proactive equipment care and ownership among operators. It aims to create a sense of responsibility for the equipment and its performance. However, WCM extends this cultural transformation across the entire organization. It promotes a culture of Continuous Improvement, involving all employees in the pursuit of excellence in every aspect of operations, even outside the boundaries of the shop floor.
Lean principles are integrated into the WCM framework, emphasizing waste reduction, efficient production flows, and the elimination of non-value-added activities. This creates a more streamlined and agile manufacturing environment.
Lean Six-Sigma: a Leaner, More Agile Approach
The evolution from classic Six Sigma to Lean Six Sigma represents a streamlined and agile methodology that combines the precision of Six Sigma with the flexibility of Lean principles. This hybrid approach is designed to eliminate waste, enhance productivity, and maintain the highest standards of quality within the manufacturing process.
Lean Six Sigma takes a more expansive view of continuous improvement, encouraging ongoing enhancements in all aspects of manufacturing, from processes and workflows to product design and operational personas. Emphasizing the elimination of non-value-added activities in processes, it aims to streamline workflows and create more efficient systems and people.
Lean Six Sigma utilizes a variety of Lean tools such as Value Stream Mapping, 5S, and Kanban, in addition to the statistical tools commonly used in Six Sigma, such as DMAIC (Define, Measure, Analyze, Improve, Control). It tends to a quicker, more agile implementation of improvements. Lean tools focus on rapid identification and elimination of waste, leading to more immediate efficiency gains. Emphasizes a customer-centric approach by identifying and delivering value as defined by the customer.
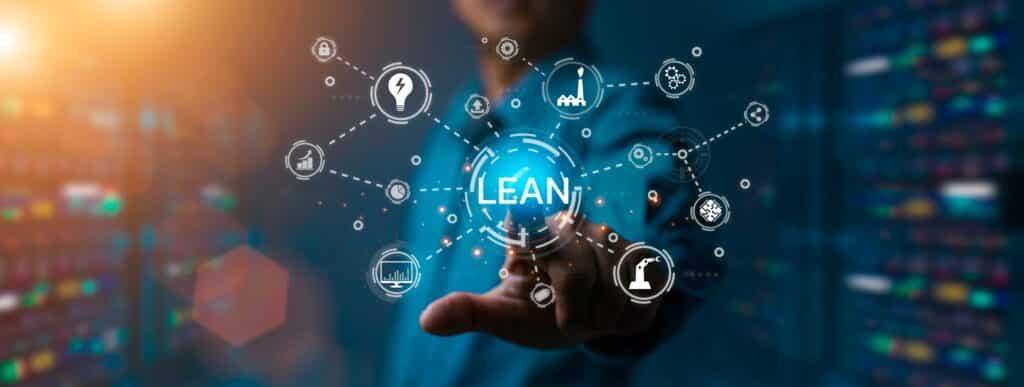
Integrated Operational Systems
Integrated systems play a crucial role in achieving Operational Excellence by streamlining processes, enhancing collaboration, and providing real-time insights. The integration of digital technologies, automation, and data-driven processes inherent in Industry 4.0 often necessitates changes and advancements in the Operational Systems of Organizations.
Real-time data analytics and Smart Manufacturing platforms are reshaping how organizations approach their day-to-day operations. Data from various departments and functions are accessible and visible to all. This visibility enables decision-makers to have a comprehensive view of the entire operation, fostering data-driven decision-making.
Integration eliminates silos and allows for the seamless flow of information across different parts of the organization. This results in more efficient workflows reduced manual data entry, and minimized delays in processes. Real-time monitoring of key performance indicators (KPIs) and operational metrics allows organizations to identify issues promptly, make informed decisions, and implement corrective actions in a timely manner.
Integrated systems facilitate collaboration among departments and teams, placing a strong emphasis on cross-functional teams that work together to address broader issues in the production process. These teams collaborate on improving efficiency, reducing waste, and enhancing overall operational performance. As an example, OEE is part of the performance metrics but extended to cover the entire value chain, ensuring that all processes contribute to Overall Efficiency. This integration can extend optimizing the whole Supply chain, reducing lead times, minimizing stockouts, and improving overall Supply Chain Efficiency.
Developing Your Own System
Organizations are increasingly developing their Operational Systems, drawing inspiration from Toyota’s renowned model. In the realm of production systems, few have left an indelible mark like Toyota’s Production System (TPS). Revered for its efficiency, innovation, and continuous improvement ethos, the TPS legacy offers valuable insights for organizations seeking to elevate their own production capabilities.
Traditional tools like Kanban and Poka-yoke transform to adapt to each organization’s needs and group together to develop robust and adaptive production systems. The Kaizen philosophy, in different forms and tools, encourages continuous improvement at all levels of the organization fostering a culture of constant refinement, empowering employees to identify and address inefficiencies at all levels.
Organizations have unique strategic objectives, industry-specific challenges, and compliance standards. Developing an in-house tailored Operational Excellence system allows them to align processes with their goals. This alignment ensures that the whole of operations and the unique culture and values cultivated, will be key enablers of the company’s mission and vision.
Indeavor Enabling Change
Reshaping Workforce Management (WFM), Indeavor serves as a bridge between traditional Operational Excellence systems and the new era. People Operations Platform offers real-time scheduling, skill-based assignments, comprehensive analytics, and integration with other enterprise systems. Indeavor aligns with the broader goals of modern Operational Excellence trends, facilitating a seamless transition for large enterprises, whereas its commitment to staying at the forefront of technology ensures alignment with these digital advancements.
Leading WFM Software for Industrial Environments
Scheduling front-line workers in Industrial environments is not easy. Indeavor, automates this process, based on your organization’s needs, employee population, and work rules, creating demand-driven, fully Automated Employee Scheduling.
The use of Engage mobile app to view schedules, see leave balances, request vacation, report a call off, volunteer for overtime, swap shifts, update contact information, and be notified of approved vacations, eliminates paper processes and grants the convenience for employees to plan their lives around work. Ensuring that compliance, work, and scheduling rules are always followed during the employee scheduling process end to End, from ERP to payroll. Encouraging open communication and cross-functional collaboration allows for a holistic approach to problem-solving and innovation.
Integrating With Enterprise Systems
Leveraging technology to create interconnected operational systems, Indeavor purpose-built APIs connect static, enterprise data to enable real-time decisions, labor planning, & optimization for the operational front-line workforce. Seamless integration with these systems ensures a unified approach to workforce optimization, maintenance, training, and improvement strategies.
This further complements Lean Six Sigma and Continuous Improvement by providing tools for streamlined communication, data-driven decision-making, and efficient workforce deployment. Indeavor integrates with Human Capital Management (HCM), Enterprise Resource Planning (ERP), Learning Management Systems (LMS), and other enterprise systems to make unique labor data easy to interpret and act upon. There is no need to overhaul existing systems and processes to capture detailed people metrics and analytics.
Managing Skills and Qualifications
The evolving landscape necessitates a shift in the skills required for operational excellence. While traditional engineering and hard skills remain crucial, the focus is shifting towards soft skills, tech-savvy operators, digital troubleshooting capabilities, and familiarity with field tools and apps. Indeavor supports this evolution by creating a skills framework across facilities, departments, locations, and employees. Maintaining proactive compliance by evaluating employee skills and job requirements at the point of scheduling, adds visibility into employee upskilling and reskilling progress via competency levels and employee skill status.
Indeavor Qualifications and Skills management improve visibility in all levels of teams’ skill levels, engaging employees and incorporating this powerful dataset into the core scheduling activity. Upskilling improves productivity by tying self-improvement to organizational efficiency. This product also allows easy integration with Learning Management and Skill Management systems, which allows hands-off management of qualifications in a constantly changing environment.
Conclusion
As manufacturing and energy markets continue to evolve, the integration of Operational Excellence strategy with the latest industry trends is imperative. Indeavor WFM solutions not only align with these trends but also provide a robust platform for large enterprises to navigate the complexities of a fast-paced market, moving from traditional TPM to WCM, Lean Six Sigma, integrated systems, and digital platforms.
The emphasis is on creating a culture of Continuous Improvement and Operational Excellence, by embracing a customer-oriented and human-centric approach. Indeavor supports this evolution by providing the tools needed for workforce coordination, skill-based scheduling, and performance analytics, embarking on a journey toward efficient, but also adaptable systems to the ever-changing demands of the market.
About the Author
Nikolas Kapsalis is a chemical engineer, MBA, and Six Sigma black belt. With two decades of operations and supply chain expertise, he has led large and diverse groups of people and managed a broad portfolio of projects. He is passionate about driving value through digital transformation. To learn more or get in touch, connect with Nikolas on LinkedIn.