Managing labor costs is a complex challenge, especially in food processing facilities where production quotas, tight deadlines, and fluctuating demand create unpredictable labor needs. These pressures often leave managers scrambling to fill gaps at the last minute, making it difficult to keep costs under control.
This reactive approach can result in scheduling inefficiencies, such as assigning higher-paid employees to fill gaps when equally qualified, lower-cost workers could step in. Additionally, in the rush to address shortages, frontline managers may overlook employees’ hours, leading to accidental overtime pay when workers who have already logged 40 hours are called in.
Overtime often becomes the default solution to staffing shortages, but this quick fix can lead to hidden costs that affect both profitability and employee well-being. Effective labor demand planning is key to avoiding this. By aligning workforce schedules with actual demand, food processors can reduce reliance on overtime, streamline operations, and improve overall cost efficiency.
The Direct Cost
According to the U.S. Bureau of Labor Statistics (BLS), the median hourly pay for a food processing worker is around $18. With overtime pay typically at 1.5 times the hourly wage, this brings the overtime rate to $27 per hour. If a worker is asked to take on an additional 8-hour shift beyond their regular 40 hours, that’s an extra $216 for the week.
While $216 might not seem like much, it snowballs quickly when overtime becomes routine. Over the course of a month, that adds up to over $800 in overtime pay alone for a single employee—and that’s not even for your highest-paid worker.
Considering the high costs of ingredients and equipment, combined with the pressure to keep prices low to maintain a competitive advantage, the food processing industry operates on thin margins. That’s why it’s important to optimize labor costs and streamline operations to avoid unnecessary overtime expenses and improve overall efficiency. Plus, time and a half isn’t the only “cost” of relying on overtime…
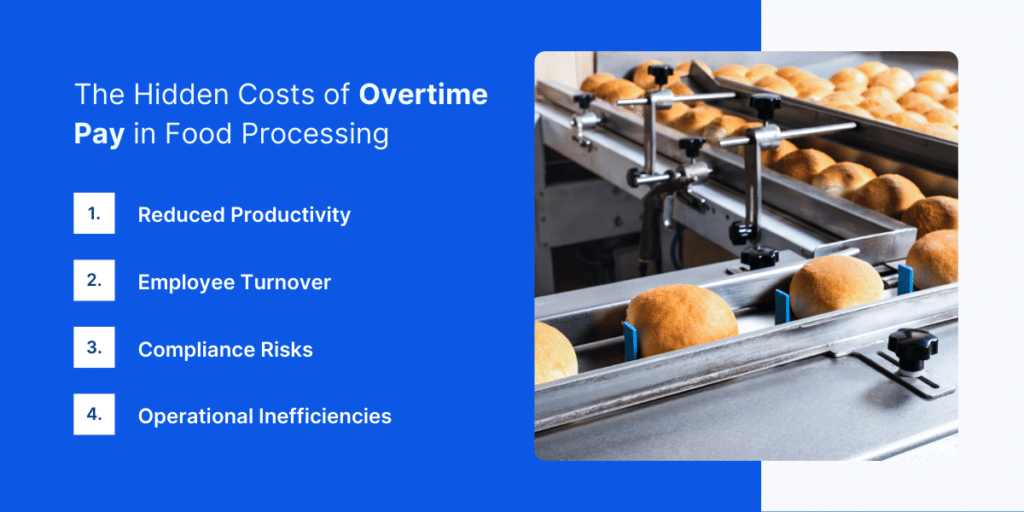
The Hidden Costs
1. Reduced Productivity
Workers fatigued by extended hours may experience a decline in efficiency and quality, leading to:
- Errors: Fatigued workers are more prone to mistakes, such as miscalculating measurements or mislabeling products, which can result in quality issues or safety concerns.
- Recalls: Mental and physical exhaustion can cause missed quality checks or improper handling of materials, leading to product defects or contamination risks that trigger costly recalls.
- Slower Production: Tired employees take longer to complete tasks, reducing throughput and overall efficiency on the production line, potentially delaying deliveries and affecting demand.
Consider this: a single food recall can result in a $10 million loss for your business.
2. Employee Turnover
Constant overtime can lead to employee exhaustion, higher turnover rates, and decreased job satisfaction, which in turn results in:
- Additional Recruitment: As burnout leads to higher turnover, you’ll incur costs for hiring and onboarding new employees, disrupting operations and increasing HR-related expenses.
- Training Costs: New employees require time and resources for training, which adds to operational costs and reduces productivity as staff are brought up to speed.
Gallup estimates that replacing leaders and managers costs around 200% of their salary, replacing professionals in technical roles costs about 80% of their salary, and replacing frontline employees can cost as much as 40% of their salary.
3. Compliance Risks
Food processing companies must adhere to labor laws, and excessive overtime can lead to unintentional violations of wage and hour regulations, resulting in costly fines or legal issues. This can include:
- Overtime Violations: Failure to properly track and compensate overtime hours may result in wage claims or lawsuits from employees, leading to legal costs and penalties. Failing to adhere to union contracts that outline overtime stipulations for certain employees can also expose companies to legal action. Even unintentional violations of union agreements can result in costly grievances, arbitration, or litigation.
- Penalties for Non-Compliance: Food processing companies may face fines from regulatory bodies like the Department of Labor (DOL) for violations of wage and hour laws, including failure to pay overtime correctly. These fines can add up quickly, reaching thousands of dollars per violation.
According to the DOL, any overtime violation (as outlined in Section 203 of the Fair Labor Standards Act) results in a $1,373 civil penalty. Repeated or willful overtime violations (as outlined in Section 207) can lead to a $2,451 penalty.
4. Operational Inefficiencies
An overreliance on overtime pay may signal that labor demand planning is not optimized, leading to inefficient use of staff and resources. Overstaffing during non-peak times or relying on costly overtime to fill gaps can result in:
- Underutilization of Employees: Not scheduling employees based on actual demand can cause operational slowdowns, as workers may be over- or underutilized, resulting in wasted labor costs.
- Wasted Resources: Inefficient allocation of resources such as equipment or materials can increase operating costs, reducing profitability.
- Disruptions in Workflow: Constant overtime may disrupt natural workflow, causing unnecessary downtime or coordination issues as workers transition between shifts.
Indeavor Helps Reduce Overtime
We did the math, and the impact of reducing overtime has been shown across multiple organizations leveraging Indeavor’s workforce management solutions.
Across our manufacturing customers as a whole, we have seen a continuous decrease in overtime rates—from an average of 8.5% in early 2023 to approximately 6% today, marking a decline of nearly 30%. In absolute terms, overtime hours decreased from around 1.3 million hours per month to just 400K hours within this period.
This 900K reduction in monthly overtime hours across our customer base translates into significant cost savings. Assuming an $18 median hourly pay, overtime would be an additional $9 per hour—that’s $27 in overtime pay for every extra hour worked. This resulted in total labor cost savings of approximately $24.3 million per month for our food processing customers.
These savings can be reinvested into (cross-) training employees, or leveraged across critical areas like equipment upgrades, market expansion, or other strategic initiatives to enhance operational efficiency and competitiveness.
Success Story: Global Fortune 100 Food & Beverage Manufacturer
One of the world’s largest food and beverage manufacturers was confronted with excessive overtime that inflated costs and strained their workforce. The company sought a more efficient approach to scheduling and labor allocation, so they contacted Indeavor.
Upon implementing Indeavor at one of their global production sites, they achieved a staggering 50% reduction in total overtime hours, cutting down from approximately 10,000 hours per month to 5,000. Overtime decreased from an average of 9.6% of total hours worked in early 2023 to around 4.5% by late 2024—a drop of more than 5 percentage points.
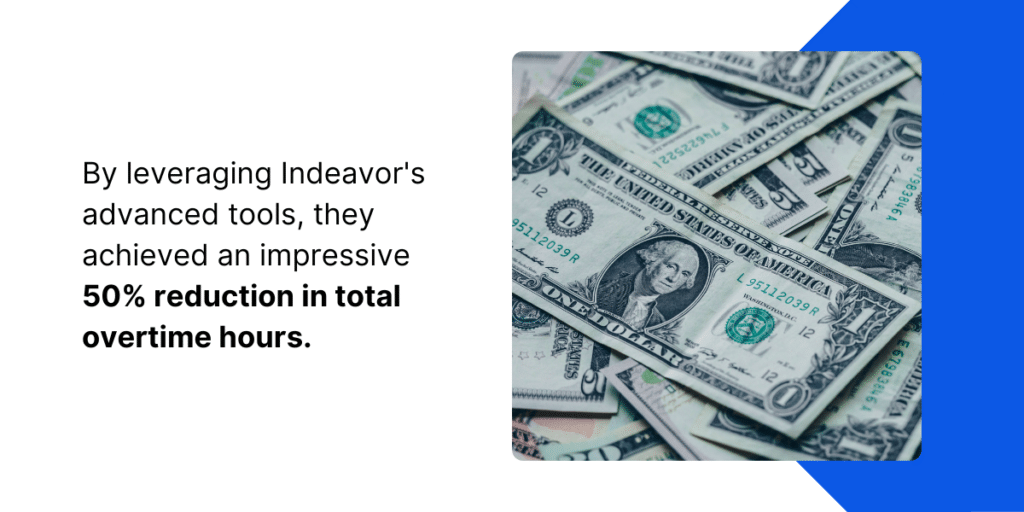
Again, using the median hourly pay of $18, the monthly reduction of 5K overtime hours translates into overtime pay savings of $135K per month. That’s $1.62 million per year.
For large, multi-facility manufacturing companies with thousands of employees, the effects of a centralized employee scheduling software help reap economies of scale benefits. By streamlining scheduling across all locations, companies can ensure that staffing levels are optimized in real-time, minimizing unnecessary overtime pay, reducing labor costs, and improving operational efficiency. As a result, organizations can not only reduce their financial burdens but also enhance workforce satisfaction and productivity, driving long-term success and growth.