Food recalls have increased 10% since 2013—with meat and poultry incidents, in particular, soaring 67%—according to a report released by the U.S. PIRG Education Fund.
We’ve previously discussed how human error in food manufacturing is a public health issue. Food processors have safety-driven guidelines to follow because it’s not just about the safety of the workers, but also the public; even one person getting sick is too many.
But even with all the regulations, there are still hundreds of food recalls every year.
This boils down to having an inadequate scheduling and staffing strategy, where plant managers are forced to be more focused on “just getting bodies on the line” due to unexpected absences as opposed to “having the right people, in the right place, at the right time”. Let’s put it this way: How many times are underqualified employees at your plant doing a job they don’t have clearance for because it was hard to find a qualified person in 5 minutes?
Proper staff training is a crucial component of food safety, but that is all for naught when you can’t easily match a particular job on the line with the employee that has the most optimal skillset. To further aid in the avoidance of food recalls, you need an automated scheduling solution with an easily accessible qualification management system.
Before the Right Scheduling Tool…
…shift managers and schedulers are stuck without an automated backup plan, leaving them exposed to risk.
When relying on Excel spreadsheets, paper, or whiteboards, shift managers are typically learning moments before the shift is due to start that there is an absence—or, on the flip side, that there are way too many employees scheduled and that they are hemorrhaging money. In the event of an absence, managers either scramble to find a body that is (fingers crossed) qualified, or they are forced to not run that line. Obviously, most will take their chances with the former. No company wants to completely halt a day’s worth of production, particularly in an industry with such intense demand.
So, they are left sifting through stacks of paper while trying to remember complex union and FLSA rules. As they’re trying to decide who the best person to fill in would be, the manager is also hoping their database has the most up-to-date number of hours their employees have worked—they wouldn’t want a hefty fine or to risk employee fatigue, after all.
You’ve probably already noticed that there is a lot of hope involved in this process. The good news is that it doesn’t have to be this way.
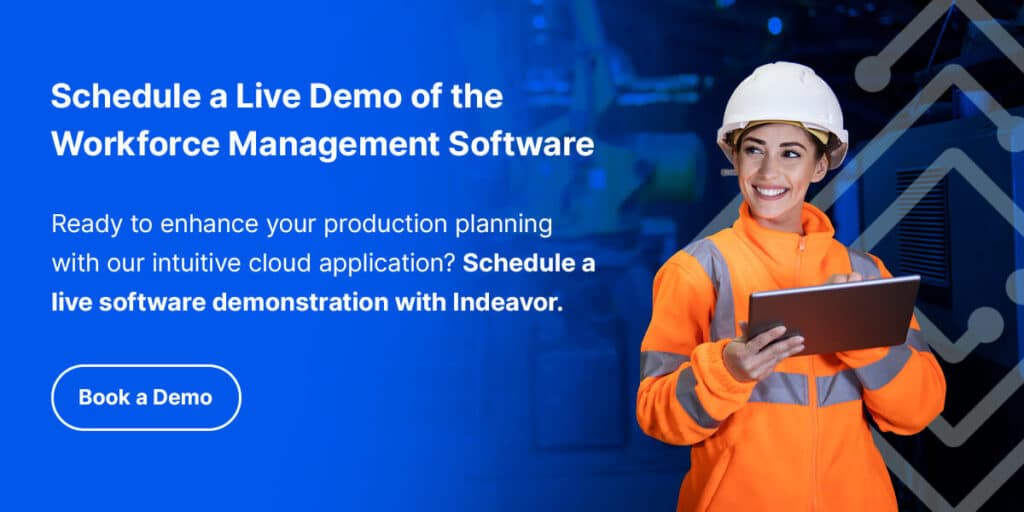
After the Right Scheduling Tool…
…you’ll have the most qualified person filling in on the line, with a quick click of a button!
There’s also a lot less finger-crossing. Here’s how it works.
Rather than finding out onsite that someone called in sick, the manager would have received an immediate notification on their mobile device. The most qualified, available person would then be assigned to that vacancy thanks to the qualification management system (QMS) that automatically compiles a skills matrix and certification tracker for every hourly employee.
Even in a case where no one calls in sick and we are strictly talking about scheduling, the tool will automatically create the most optimal shift roster based on internal and external rules, hours worked, and the skills matrix.
Qualification management—and simply having centralized access to the certifications of all your hourly employees in general—is critical. Plant managers can rest assured that they are filling an empty position on the line with the most capable person who can adhere to those food contamination guidelines. This system is the most granular and widespread system a facility could use.
Employee scheduling is the lifeblood of the facility, so it should come as no surprise that this will be one of the only systems that every employee will use everyday.
Learn About Our Workforce Management Solution
Our workforce management SaaS solution which offers clients an end-to-end, cloud-based employee scheduling, time & attendance, and absence management system. Integrate with your human capital management and enterprise resource planning systems to create a robust platform that provides you with real-time employee data.
Interested to see how we can help your plants reduce food recalls enterprise-wide? Click here to request a demo.