An analysis of 2020–2024 Food and Drug Administration (FDA) data conducted by Food Safety Magazine yielded startling results. Food recalls increased over 20% between 2020 and 2023, with no signs of slowing down. Based on the first half of 2024, the number of total recalls is projected to roughly match 2023’s.
Allergen contamination (~40%) was the leading cause of recall. This is often due to cross-contamination and improper labeling during manufacturing. Bacterial contamination was responsible for about 21% of all cases, followed by foreign object contamination (~11%).
The common denominator? These incidents could have been prevented with consistent employee training and the effective management of their skills and competencies. It could mean the difference between seamless operations and costly product recalls that threaten public health.
Did we mention that the average cost of a recall is $10M?
Why are Skills and Competencies Important?
Skills and competency management involves identifying, tracking, and optimizing the abilities and knowledge of the workforce to ensure they meet industry standards and can adapt to evolving demands.
Skills and competencies may be used interchangeably, but there is nuance. Skills refer to the specific abilities or proficiencies that an individual can develop through practice and experience, such as operating machinery or conducting quality control tests. Competencies encompass not only these skills but also the knowledge, behaviors, and attributes required to perform a job effectively, such as problem-solving, communication, and adherence to safety protocols.
Both must be kept in mind at the point of scheduling. Ensuring that the right person is in the right role at the right time is not just a matter of operational efficiency—it’s a matter of public safety, compliance, and overall product quality.
Historically, many organizations have struggled with—or outright neglected—comprehensive tracking of these essential skills. Instead, they rely on traditional, often manual, methods that fail to capture the full scope of employee capabilities. This is where modern scheduling solutions, integrated with robust skills and competency management, play a pivotal role.
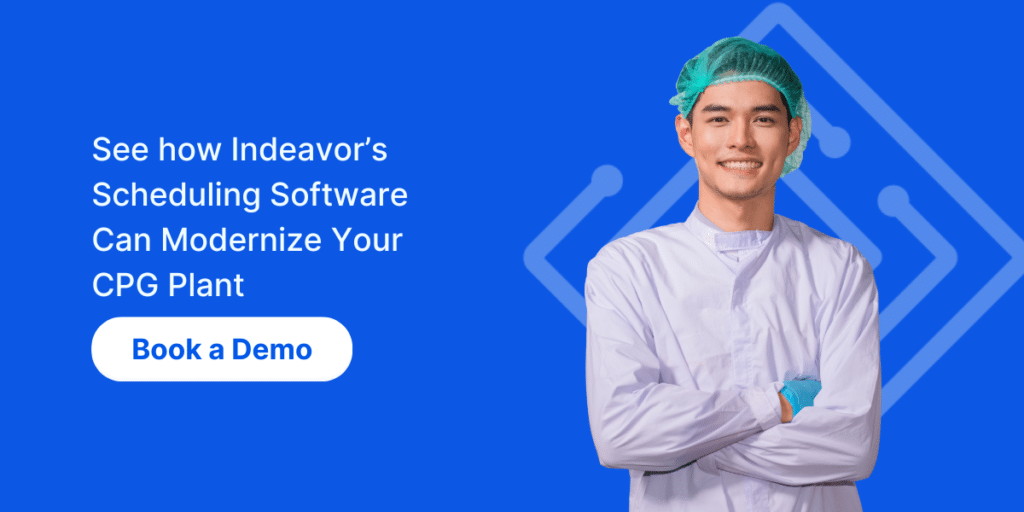
Challenges and Solutions
Manual Tracking
The first major issue is the sheer volume and diversity of skills that need to be monitored. Employees at a food processing facility must master a wide range of skills, from the technical know-how required to operate sophisticated machinery to the detailed understanding of food safety regulations and protocols. As these skills evolve and expand, keeping track of each employee’s capabilities manually becomes increasingly untenable.
Outdated systems, often paper-based or reliant on simple spreadsheets, are prone to human error, such as incorrect data entry, lost records, or failure to update information in a timely manner. These errors can accumulate over time, leading to a distorted picture of the workforce’s actual capabilities. For instance, if an employee’s certification in handling allergens expires but the record isn’t updated, that employee might be incorrectly scheduled for tasks involving allergens, putting the company at risk of a safety violation and potential recall.
Manual processes lack the dynamic functionality needed to integrate with other operational systems, such as scheduling software. This means that decisions regarding employee deployment may be made based on incomplete or outdated information. For example, a manager might unknowingly assign a task requiring a specific certification to an employee who lacks it, simply because the spreadsheet hasn’t been updated. This can lead to inefficiencies, with employees being assigned to roles for which they are not fully qualified, increasing the risk of errors, non-compliance, and ultimately, product recalls.
To overcome this, companies need to adopt a more systematic and proactive approach to skills and competency management. Rather than rely on manual updates, they should leverage digital tools that provide real-time tracking and management of employee skills. These platforms can automatically update employee records, making it easier to identify skills gaps or expiring certifications to ensure that the right employees are scheduled for the right tasks. By integrating these tools with scheduling systems, companies can optimize workforce deployment, reduce the likelihood of errors, and improve overall efficiency.
Pro-tip: Better yet, having a comprehensive workforce management system that is driven by skills-based scheduling helps facilities incorporate scattered systems of record in one location. This holistic view ensures that all aspects of employee qualifications are accounted for and aligned with operational needs.
Changing Regulations
The dynamic and ever-evolving nature of regulations in the food processing industry presents a significant challenge in maintaining a well-trained and compliant workforce. Regulatory bodies like the FDA and USDA frequently update guidelines and introduce new standards to ensure food safety, often in response to emerging risks, technological advancements, or changes in public health priorities. These shifts require companies to be agile in updating their processes and ensuring that their employees are equipped with the latest knowledge and skills.
A lack of standardized training programs exacerbates these issues. Without a unified approach to training, employees in different locations may receive varying levels of information and guidance. This can lead to significant disparities in skill levels and understanding of regulatory requirements, further complicating the management of competencies across the organization. The risk here is not just non-compliance, but also the potential for critical errors that could lead to food safety incidents and recalls.
Plus, the pace of regulatory changes can outstrip an organization’s ability to respond effectively, especially if they rely on traditional or manual training methods. Developing, deploying, and monitoring training programs in response to new regulations can be time-consuming. By the time these programs are fully implemented, regulations might have evolved yet again, leaving a perpetual gap between what is required and what is actually practiced.
To mitigate these challenges, companies need to adopt more flexible and scalable training solutions that can be quickly updated and distributed across all facilities. Digital learning platforms that allow for real-time updates to training materials and provide consistent, standardized training experiences across the organization can be a powerful tool. These platforms can also offer tracking and assessment features, ensuring that all employees are not only trained but also competent in applying new regulations in their daily work.
Pro-tip: Invest in a scheduling platform that easily integrates learning management (LMS), talent management (TMS), and human resource information (HRIS) systems to add visibility into employee upskilling and reskilling opportunities and progress.
Employee Turnover
Finally, there is often a disconnect between the skills needed and those that are available within the workforce. Food processing is known for its high employee turnover rates—the manufacturing industry in general has a roughly 40% turnover rate—which exacerbates the skills gap.
When experienced employees leave, they often take with them a wealth of knowledge and specialized skills that are not easily replaced. This loss of expertise can leave a void in the workforce, making it difficult to maintain the same level of operational proficiency and adherence to safety standards. For example, an experienced machine operator may have nuanced knowledge of how to troubleshoot specific equipment issues—knowledge that a new or less experienced employee might lack. This can lead to inefficiencies, increased downtime, and even safety hazards.
The process of replacing the skills lost due to turnover is often slow and challenging. It’s not always possible to recruit new employees who possess the exact skills required, particularly in an industry that demands a combination of technical expertise, adherence to strict safety protocols, and the ability to operate specialized equipment. And new hires typically require extensive training to reach the level of proficiency of their predecessors. During this transition period, the risk of errors, accidents, and non-compliance with regulations increases, widening the skills gap.
To safeguard against the impact of turnover, companies should implement knowledge retention strategies, such as mentorship programs where experienced employees pass on their expertise to newer staff. Documentation of processes and best practices is also critical in ensuring that valuable knowledge is not lost when employees move on.
Pro-tip: Investing in continuous learning opportunities for employees is essential to close the skills gap. This includes providing access to ongoing training and development programs that keep employees updated on the latest technologies, regulations, and industry best practices. Integrating training with skills-based scheduling systems can also ensure that employees are consistently assigned to tasks that match their current skill levels, reducing the risk of errors.
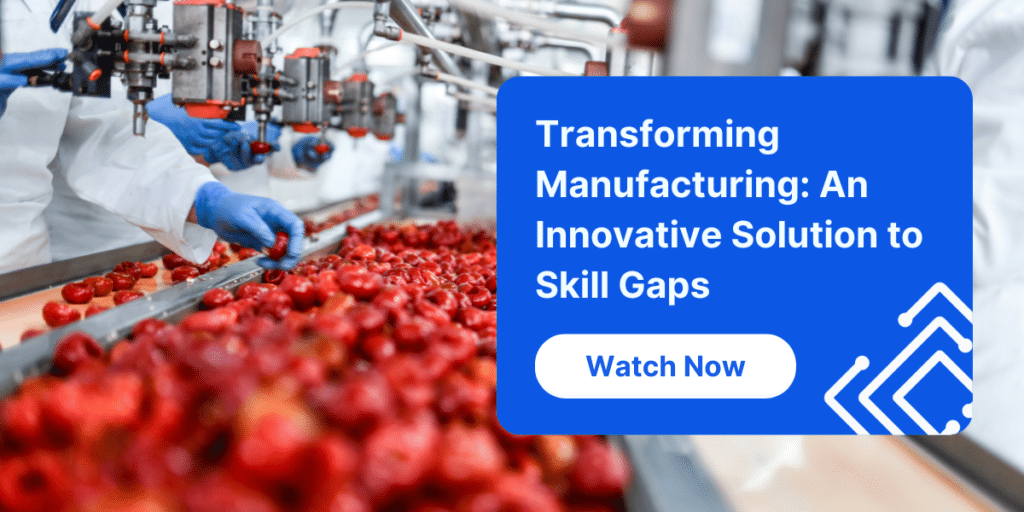
Operational Efficiency and Cost Reduction
Efficient Utilization of Resources
When employees are well-trained and proficient in their roles, they can perform tasks more effectively and with greater precision, which minimizes the time and materials required to produce quality products. For instance, employees who are knowledgeable about proper handling and storage techniques can prevent spoilage and contamination, which directly contributes to reducing waste and ensuring that resources are used as efficiently as possible.
The efficient use of resources extends beyond just the physical materials and includes time management as well. Skilled workers are better at multitasking, problem-solving, and decision-making, all of which contribute to a more streamlined operation. When employees know how to use tools and equipment correctly and understand the processes they are involved in, they can complete tasks faster and with fewer mistakes, which further enhances overall operational efficiency.
Reduced Waste and Increased Productivity
One of the most significant benefits of having a skilled workforce is the reduction of waste, which directly impacts cost savings. In food processing, wastage can occur at various stages, from raw material handling to packaging. For instance, improper cutting techniques can lead to excessive waste of raw ingredients, while incorrect storage practices can result in spoilage. Employees who are trained to handle materials correctly and who understand the importance of minimizing waste can help reduce these losses significantly.
Increased productivity is another direct result of reduced wastage. When employees work efficiently and with minimal errors, production lines can operate at their full potential, leading to higher output levels. This increase in productivity not only meets demand more effectively but also reduces the per-unit cost of production, allowing companies to operate more profitably. As waste is minimized, the need for rework or disposal of spoiled products decreases, further contributing to a more efficient operation.
Cost Savings
The financial implications of a skilled workforce extend to cost savings achieved through streamlined processes and reduced errors. Every error in food processing—whether it’s a mislabeling incident, a machine malfunction, or a contamination event—can lead to costly delays, product recalls, and even legal issues. Skilled employees are better equipped to avoid such errors by adhering to best practices and proactively identifying potential issues before they escalate.
Streamlined processes, driven by a competent workforce, reduce the need for constant oversight and intervention from management. When employees are confident in their roles and understand how to perform their tasks efficiently, the workflow becomes more consistent and predictable. This consistency reduces the likelihood of disruptions and ensures that production schedules are met, which in turn minimizes overtime costs and other expenses related to inefficiencies. Additionally, fewer errors mean less waste, fewer recalls, and lower costs associated with corrective actions, all of which contribute to significant cost savings for the company.
Adaptability to Technological Advancements
Incorporating new technologies into food processing operations is a critical step for companies aiming to stay competitive in an increasingly complex and regulated industry. Technologies like automation, AI, and advanced data analytics offer significant benefits, including improved efficiency, enhanced product consistency, and reduced operational risks. However, successfully integrating these technologies requires more than just the right tools—it requires a workforce that is skilled, adaptable, and capable of leveraging these innovations to their full potential.
Even the most advanced robotics or AI systems can fall short if your workforce scheduling isn’t optimized to match the skill sets needed to operate them efficiently.
This is where Indeavor makes a transformative impact. Indeavor provides a comprehensive workforce management solution that ensures the right employees are aligned with the right tasks at the right time, maximizing the potential of your technological investments. By automating workforce scheduling—including real-time changes like shift swaps and absences—Indeavor enables companies to optimize their operations, reduce errors, and maintain high standards of safety and quality.
This is because only employees with the right skills and competencies will be assigned to each job, every time; when last-minute changes to the schedule inevitably occur, only qualified employees will have the option to fill in or volunteer for the job. Indeavor’s platform is designed to support food processing companies in their journey towards technological excellence, helping them to streamline processes and achieve greater operational efficiency.
Importance of Upskilling and Training Programs
As the food processing industry evolves, the importance of continuous upskilling and training programs becomes increasingly clear. New technologies often require new skills, and employees must be trained not only to use these technologies effectively but also to understand the broader implications for their roles and the company as a whole.
Indeavor plays a crucial role in this aspect by offering robust tracking capabilities for upskilling and training initiatives. Through powerful integrations with LMS, TMS, and HRIS, Indeavor provides visibility into employee progress and ensures that training programs are aligned with the company’s operational needs. This integration allows companies to monitor the development of their workforce in real-time, ensuring that employees are continuously updated on the latest technologies and industry practices.
By leveraging Indeavor’s ability to track and manage training initiatives, food processing companies can ensure that their workforce remains competent, compliant, and ready to meet the demands of a rapidly changing industry. This not only enhances the company’s ability to incorporate new technologies but also positions it as a leader in the industry, with a workforce that is skilled, adaptable, and equipped for the future.
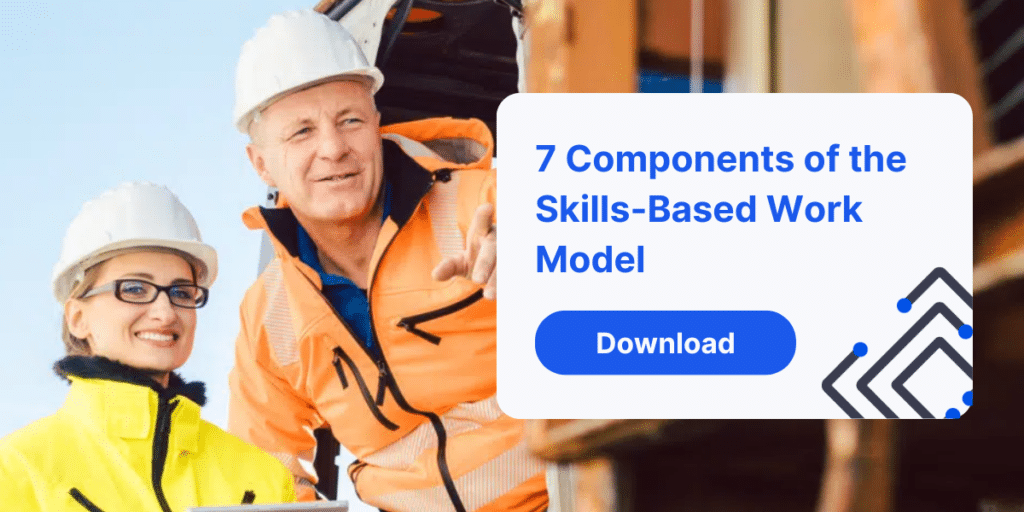
Now is the Time to Prioritize Skills and Competency Management
The success of a food processing company hinges on its ability to effectively manage the skills and competencies of its workforce. In an industry where the stakes are incredibly high—ranging from public health risks to substantial financial penalties—ensuring that employees are well-trained, adaptable, and capable of meeting the demands of the job is crucial. Skills and competency management is not just a matter of operational necessity; it is a strategic imperative that can drive innovation, improve efficiency, and enhance competitiveness.
Indeavor’s Skills Management Solution is designed to address these critical needs by providing a robust platform that helps companies identify, track, and optimize the skills of their workforce. Through seamless integration with other operational systems, Indeavor enables companies to maintain a real-time, comprehensive view of their employees’ competencies, ensuring that the right skills are always available when and where they are needed most. This not only helps in aligning the workforce with the dynamic requirements of the industry but also supports continuous development through targeted upskilling and reskilling initiatives.
With Indeavor, both skills and competencies are kept in mind at the point of scheduling—automatically.
As regulations continue to evolve, companies must prioritize skills development and management to stay ahead of the curve. Indeavor’s solution simplifies this process, allowing companies to efficiently manage compliance, reduce risks, and enhance operational effectiveness. Now is the time for food processing companies to take proactive steps in developing their workforce and ensuring that they are equipped to handle the complexities of the industry.