Logistics is the backbone of the transportation industry. Whether it’s coordinating shipments for third-party logistics providers (3PLs), managing fleets of trucks across sprawling networks, or ensuring punctuality in public transit systems, the success of these operations hinges on one critical factor: logistics scheduling.
Logistics scheduling is the process of planning, organizing, and optimizing the movement of goods, resources, and personnel to ensure timely and efficient operations. It involves coordinating routes, delivery timelines, workforce shifts, and equipment usage while accounting for factors like demand variability, traffic, and compliance with labor laws.
Effective scheduling determines how well businesses can deliver on time, reduce costs, and adapt to unforeseen challenges. For industries like trucking, 3PLs, and public transit, poor scheduling is more than an inconvenience—it can lead to customer dissatisfaction, unnecessary expenses, and even safety risks. Adopting modern scheduling solutions can create a competitive edge.
Benefits of Effective Logistics Scheduling
When done well, logistics scheduling unlocks significant benefits for transportation organizations:
- Operational Efficiency: By optimizing route planning and aligning schedules with demand, organizations can reduce vehicle idle time, minimize fuel costs, and improve overall resource utilization.
- Improved Customer Satisfaction: Timely deliveries and real-time updates enhance customer experiences, which is especially critical in the highly competitive logistics space.
- Cost Savings: Effective scheduling minimizes overtime costs, avoids last-minute adjustments, and reduces wear and tear on vehicles by creating smarter plans.
- Compliance and Safety: Adhering to labor laws, such as Hours of Service (HOS) regulations, and reducing driver fatigue through proper scheduling ensures both legal compliance and safety—for employees and the public.
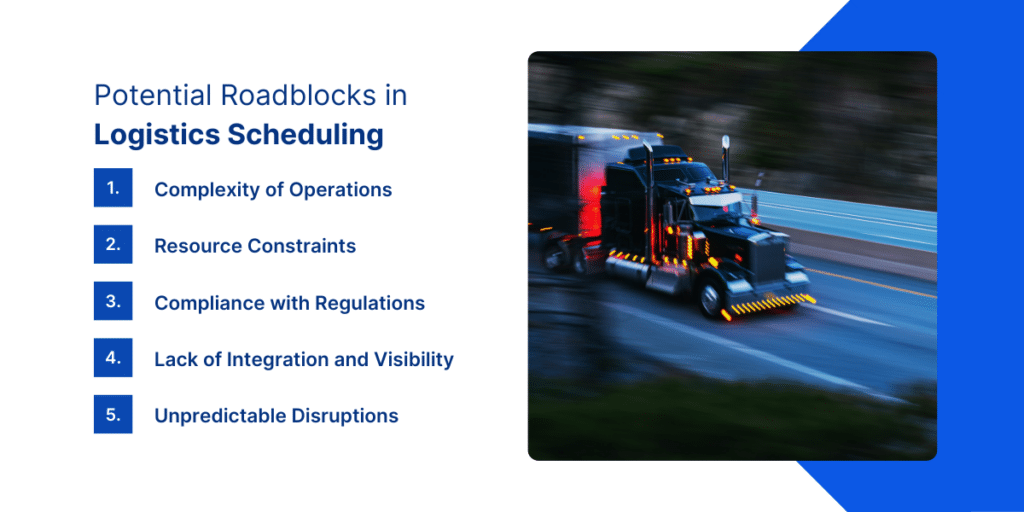
Roadblocks to Success
To reap these benefits, you need to overcome many obstacles. Logistics scheduling is a balancing act that requires careful coordination of resources, timelines, and external variables. Here are the major challenges faced by organizations today.
Complexity of Operations
Logistics scheduling involves juggling numerous moving parts, often across large fleets, diverse routes, and fluctuating demand. Organizations must contend with dynamic variables such as traffic congestion, weather disruptions, and last-minute delivery requests, all of which can derail even the best-laid plans. The interdependence of tasks like coordinating shipments, vehicle availability, and driver schedules adds further complexity.
For businesses operating under tight timelines, a single misstep can lead to missed deadlines, dissatisfied customers, and financial penalties. Navigating this intricate web requires precision and flexibility, both of which are difficult to achieve without modern tools.
Resource Constraints
The transportation industry faces significant resource challenges, particularly driver shortages, which force businesses to make tough decisions about scheduling priorities. Vehicles also require regular maintenance, creating unplanned downtime that can disrupt operations. Limited budgets add another layer of difficulty, as organizations must minimize overtime and fuel costs while still meeting delivery expectations.
These constraints make it harder to optimize schedules and maintain efficiency. As a result, resource limitations often act as a bottleneck, preventing companies from scaling effectively.
Compliance with Regulations
Labor and safety regulations impose strict constraints on logistics scheduling, with violations leading to penalties and safety risks. Hours of Service (HOS) rules limit the number of hours a driver can work, forcing planners to be meticulous in their scheduling. The following HOS rules are designed to prevent fatigue-related accidents, ensuring drivers get adequate rest while maintaining compliance with federal safety standards:
- Driving time limit: Drivers can drive for a maximum of 11 hours after they have had 10 consecutive hours off duty to rest.
- On-duty time limit: Drivers cannot drive beyond the 14th consecutive hour after starting their on-duty period, even if they haven’t reached the 11-hour driving limit.
- Break requirement: Drivers must take a 30-minute break if they have driven 8 cumulative hours.
Noncompliance may result in fines of up to $11,000 per violation for drivers. Employers can face fines of up to $16,000 per violation. Union agreements or contractual obligations in public transit systems further complicate shift planning and overtime management.
Lack of Integration and Visibility
Many transportation organizations still rely on disjointed systems and manual processes, creating inefficiencies that ripple through their scheduling efforts. Separate tools for fleet management, workforce planning, and route optimization often result in data silos and communication breakdowns.
Without a centralized, real-time view of operations, dispatchers and managers struggle to coordinate effectively, leading to delays and errors. Manual scheduling methods are especially prone to mistakes and slow response times, further exacerbating the problem. These challenges make it difficult to achieve the level of precision and adaptability required in modern logistics.
Unpredictable Disruptions
Despite the best planning, unforeseen events frequently upend schedules, requiring rapid adjustments. Natural disasters such as floods, snowstorms, or hurricanes can cause widespread delays and cancellations. Last-minute changes from customers, such as expedited delivery requests, add to the unpredictability. Economic factors like fluctuating fuel prices or sudden demand surges can strain resources and derail schedules. These disruptions demand a level of agility that many companies find hard to achieve with traditional scheduling approaches.
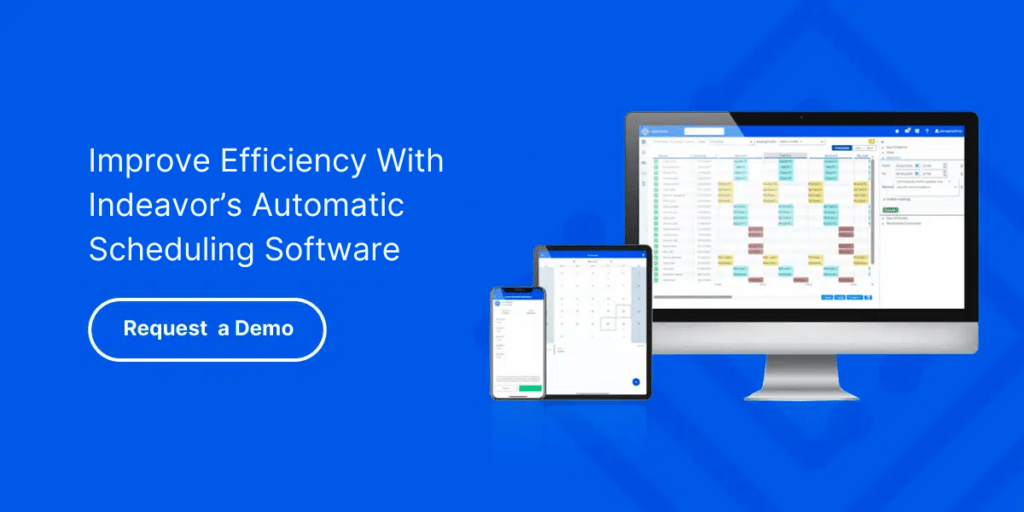
Paper Processes: The Potholes on the Path to Efficiency
Relying on paper-based or manual processes for logistics scheduling is like driving on a road riddled with potholes—slowing progress, increasing risks, and causing unnecessary wear and tear. Manual methods lack the real-time adaptability needed to manage the complexities of modern transportation operations. They are prone to human error, making it easy to overlook key details like driver availability, maintenance schedules, or compliance with regulations such as HOS.
Additionally, these processes often rely on fragmented or siloed systems, resulting in communication breakdowns and delays in decision-making. Paper processes simply cannot keep up with the dynamic nature of logistics, especially when faced with sudden disruptions like weather events or last-minute customer requests. For companies striving to remain competitive, ditching these outdated methods in favor of automated, integrated solutions is not just an option—it’s a necessity.
Get on the Right Track With Indeavor
Indeavor offers a comprehensive workforce management platform designed to address all the challenges of logistics scheduling. Here’s how:
- Simplifying Complexity: Indeavor provides centralized scheduling tools that optimize resource allocation, integrate with fleet management systems, and account for real-time variables like demand fluctuations.
- Mitigating Resource Constraints: With automated labor planning, Indeavor helps transportation companies balance limited resources, schedule maintenance efficiently, and avoid costly overtime.
- Ensuring Compliance: Indeavor tracks regulatory requirements, such as HOS rules, in real time, preventing violations and ensuring safe, compliant operations. With visibility into each employee’s hours worked, supervisors and schedulers can make informed decisions to ensure compliance with HoS limits—even when faced with unexpected changes, such as shift swaps or last-minute callouts.
- Real-Time Visibility: The platform integrates data across departments, offering a single source of truth for dispatchers, managers, and drivers. This eliminates silos and ensures seamless communication.
- Adapting to Disruptions: Indeavor’s dynamic scheduling capabilities allow for quick adjustments in response to unforeseen events, ensuring minimal downtime and consistent service delivery.
With Indeavor, transportation companies can pave a smoother path to efficiency, customer satisfaction, and long-term success.
About the Author
Claire Pieper is the Digital Marketing Specialist for Indeavor. In her role, she specializes in crafting strategic and engaging content, ensuring that customers are well-informed. Claire is dedicated to enhancing the customer experience and optimizing the user journey through Indeavor’s solutions. To learn more or get in touch, connect with Claire on LinkedIn.