As global manufacturers respond to evolving supply chains, trade policies, and reshoring trends, many are build new American manufacturing operations or expand operations into new countries. While capital investments in equipment, facilities, and talent naturally take center stage, one foundational element often gets overlooked: workforce management.
Workforce Management (WFM) isn’t just a back-office function to be addressed later. In fact, organizations that implement a solid strategy and infrastructure from the start gain substantial advantages in productivity, cost savings, employee engagement, and operational agility. Here’s why it’s absolutely essential to embed workforce management into planning, tooling, and automation at the outset of any new American manufacturing operation.
1. Establish Operational Efficiency from Day One
New American manufacturing operations often face inefficiencies early on due to inconsistent staffing practices, manual scheduling, and unclear processes. A workforce management system provides structured scheduling, skills alignment, and labor demand forecasting—allowing operations to scale smoothly.
Without people operations in place, plants may experience:
- Understaffed or overstaffed shifts
- Overtime abuse and fatigue risks
- Scheduling conflicts and employee dissatisfaction
Having the right platform ensures every shift is staffed with the right people, in the right roles, at the right time.
2. Avoid Costly Retrofits Later
Trying to implement a system after a facility is up and running often leads to disruption, retraining, and the need to untangle bad habits. American manufacturing operations can lose up to $1.3 million annually due to inefficient, manual, and paper-based processes. These outdated systems lead to significant costs in labor, errors, and wasted time that could otherwise be spent on value-generating activities. By automating workflows and transitioning to more efficient digital systems, businesses can significantly reduce these losses and improve operational performance.
By integrating with technology from the beginning, American equipment manufacturing can avoid costly rework and align labor strategy with business goals from day one. Early adoption of WFM tools also enables seamless integration with other core systems (like ERP or HRIS) during the foundational tech stack buildout—avoiding future headaches.
3. Automate Labor Compliance and Fatigue Risk Management
Regulatory requirements, union rules, and fatigue management are often more complex in new markets. A workforce management solution automates rule enforcement and generates audit-ready reports, helping reduce compliance risk.
This is especially important in American manufacturing operations with strict work hour regulations or environments where safety and fatigue play a major role (e.g., food processing, aerospace, nuclear energy).
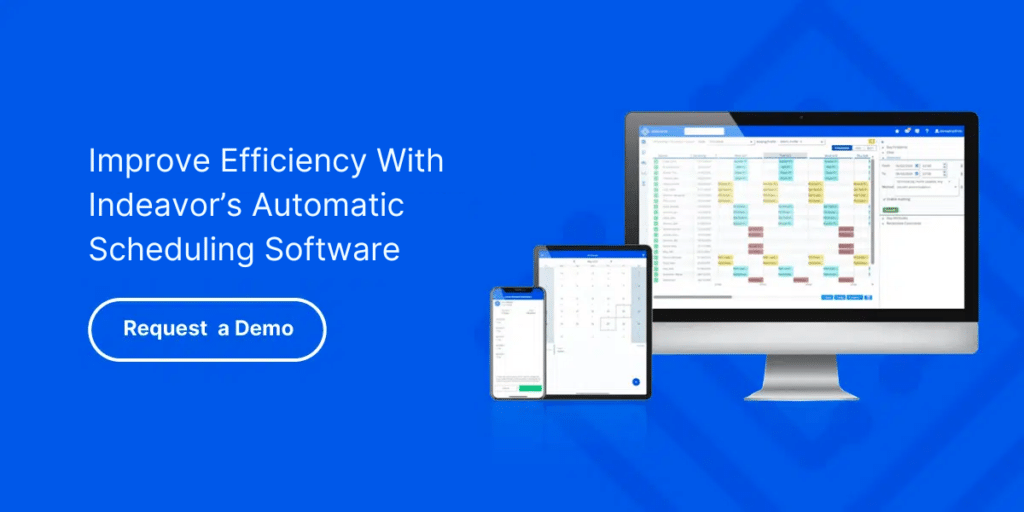
4. Use Data and Analytics to Drive Better Decisions
From the first day of operation, a scheduling platform starts collecting valuable data and analytics on labor trends, attendance, staffing patterns, and demand alignment. This enables plant managers to:
- Make data-driven staffing decisions
- Forecast labor needs more accurately
- Identify performance issues early
With embedded analytics, American manufacturers can fine-tune operations before inefficiencies become systemic.
5. Support Employee Engagement and Retention from the Start
Launching a new manufacturing facility often means hiring dozens or hundreds of new employees. Creating a positive first experience is key to long-term retention.
Mobile scheduling apps empower employees to:
- View schedules and request changes
- Swap shifts and request time off
- Receive real-time communication from supervisors
This level of transparency and autonomy leads to higher engagement, lower turnover, and a stronger workplace culture.
6. Enable Agile, Scalable Growth
As demand shifts or expansions occur, within American manufacturing, a strong foundation gives you the flexibility to adapt quickly. You can add new lines, shifts, or entire departments without reinventing your labor strategy.
For large-scale operations, where coordinating labor across multiple departments, shifts, or even facilities is critical, a robust workforce management solution provides the centralized visibility and automated scheduling needed to support consistent, efficient operations.
In American manufacturing, where production volume, compliance demands, and labor costs are significant, scaling without a unified workforce strategy can lead to fragmentation and inefficiency. A purpose-built platform enables manufacturers to align workforce resources with production goals, optimize shift coverage, and maintain quality and safety standards across the enterprise.
Whether launching a single flagship plant or multiple regional facilities. With the right system in place, growth becomes not only manageable but strategically streamlined.
Don’t Treat WFM as an Afterthought in American Manufacturing
Starting new American manufacturing operations without a workforce management plan is like building a factory without a blueprint. You might get it up and running, but inefficiencies, compliance issues, and turnover will eventually catch up. By investing in workforce management from day one—planning, tooling, automation, employee self-service, and data analytics—you lay the groundwork for long-term success.
Whether you’re reshoring production, entering a new market, or launching your first facility, make technology a core pillar of your American manufacturing strategy from the start. Request a demo today or reach out to us for more information at info@indeavor.com.