Gray collar workers are often forgotten about but hold a lot of power for the future of manufacturing. In this article, we cover the importance they hold for manufacturing. But first, it’s important to understand exactly who they are.
What is a “Gray Collar” Worker?
Gray-collar worker is a term used to describe a type of worker who isn’t a true white-collar (professional or managerial), or blue-collar (manual labor), but falls somewhere in between. Gray collar workers often have a mix of technical and professional skills, and their work typically involves both manual tasks and more intellectual or complex responsibilities. Examples of gray-collar workers include tech workers, technicians, and support staff in fields such as IT, healthcare, and manufacturing.
Gray-collar workers are typically paid somewhat less than white-collar workers, but more than blue-collar workers. They usually possess higher education or specialization when compared to blue-collar workers, but may not have the same level of management or decision-making authority as white-collar workers. In some cases, gray-collar workers also have the opportunity to advance into more managerial or professional roles over time.
Why Are Gray-Collar Workers Necessary for Manufacturing?
Spoiler alert: they bring agility, flexibility, and operational efficiency.
The future of manufacturing, given the current volatile economic situation, means that manufacturers need to involve more factors in their overall strategy, than just making existing processes more efficient. They need someone to champion it. This is where “gray collar” workers come into the picture.
White-collar workers play a vital role in manufacturing operations by providing technical expertise and flexibility. Both are necessary to ensure a smooth and efficient operation during production. Let’s go over the reasons why:
1. Technical skills. Most gray-collar workers in manufacturing possess technical skills that are crucial to the operation of the production process. They may work as technicians or technologists, for example, and be responsible for maintaining and repairing equipment, or for setting up and operating complex machinery.
2. Flexibility. Gray collar workers often possess a mix of technical and professional skills, making them more flexible and adaptable than workers who are specialized in a single area. This is useful in a manufacturing setting, where the work environment may be constantly changing.
3. Collaboration: Gray collar workers may be more likely to work collaboratively with others, as they often have a broad understanding of the various roles and responsibilities within a manufacturing operation. This helps improve communication and coordination among different teams and departments.
4. Productivity: Gray collar workers can often contribute to increased productivity in a manufacturing setting by using their technical skills to troubleshoot problems and identify efficiencies in the production process.
Overall, gray-collar workers play a vital role in manufacturing operations by providing the technical expertise and flexibility that are necessary for a smooth and efficient operation of the production process.
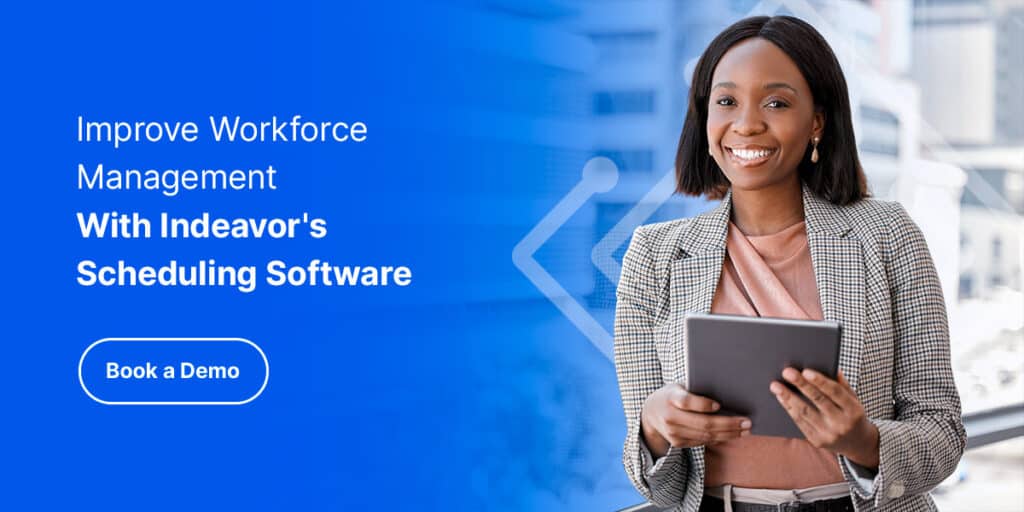
The Future of Gray Collar Workers in Manufacturing
Unfortunately, there is no crystal ball when it comes to what the future will hold for gray-collar workers. However, it’s likely that the demand for gray-collar workers will continue to grow in the coming years, as many industries continue to rely on the technical skills and flexibility – which these workers bring to the table.
Forrester listed “balancing the automation triangle to get the best from hardware, software, and people” as one of the top key trends in the future of manufacturing in late 2022. Stating, “Smart leaders are moving away from long and brittle supply chains to embrace more flexible and resilient supply networks.” We believe gray-collar workers will provide the most value in this situation, due to their flexibility and for adoption and use of automation and technology in the workplace. his may lead to some changes in the types of tasks that gray-collar workers are responsible for, as well as the need for them to acquire new skills to keep up with technological advances.
Additionally, increased focus on sustainability and eco-friendliness in many industries may also create new opportunities for gray-collar workers, as there may be a need for technicians and technologists with expertise in areas such as renewable energy or sustainable manufacturing processes.
Overall, it’s likely that gray-collar workers will continue to play a vital role in many industries, including manufacturing, in the coming years. However, they may need to adapt to changing technologies and industry trends in order to remain competitive and relevant in the job market.
Can Gray-Collar Workers Fit In With Scheduling Automation?
With their agile characteristic, gray-collar workers are the right people to help with automation in a manufacturing setting. We’ve listed a few ways in which this can happen:
1. Work with scheduling software: Gray collar workers can work with scheduling software to create and manage their schedules. This can help ensure that they are aware of their responsibilities and tasks for each shift, and it can also make it easier for them to request time off or swap shifts with other workers.
2. Use automation to streamline tasks: Gray-collar workers can use automation to streamline tasks and reduce the amount of time spent on manual tasks. For example, they may use automation to monitor and maintain equipment or to track and manage inventory, giving them time back to focus on more pertinent issues.
3. Learn new skills: Gray collar workers can learn new skills that are related to automation, such as programming or data analysis, in order to stay competitive in the job market. This can help them take on more advanced roles in their organizations and work more closely with automation systems.
4. Collaborate with automation specialists: Gray-collar workers can work closely with automation specialists to identify areas where automation can be used to improve efficiency and productivity in the manufacturing process. They can also contribute their technical expertise to the design and implementation of automation systems.
Overall, gray-collar workers can merge with schedule automation by leveraging their technical skills and expertise to work more closely with automation systems and by staying up to date with the latest technologies and trends in the industry. This mindset, combined with Indeavor’s Scheduling Software will help organizations achieve operational efficiency. Give us a call to learn more!
About the Author
Claire Pieper is the Marketing Communications Coordinator for Indeavor. She aims to share information to improve the customer journey. To learn more or get in touch, connect with Claire on LinkedIn.